In today's fast-paced world, speed matters. This is especially true in construction.Whether it’s a new hospital wing, a state-of-the-art university building, or a major retail expansion, getting projects completed faster has never been more critical. Owners want to move in quickly, start generating revenue, and meet growing demands. But delivering a project on an accelerated timeline isn’t as simple as just working faster. It takes strategic planning and collaboration, technology, and an open mind to rethink traditional construction methods. |
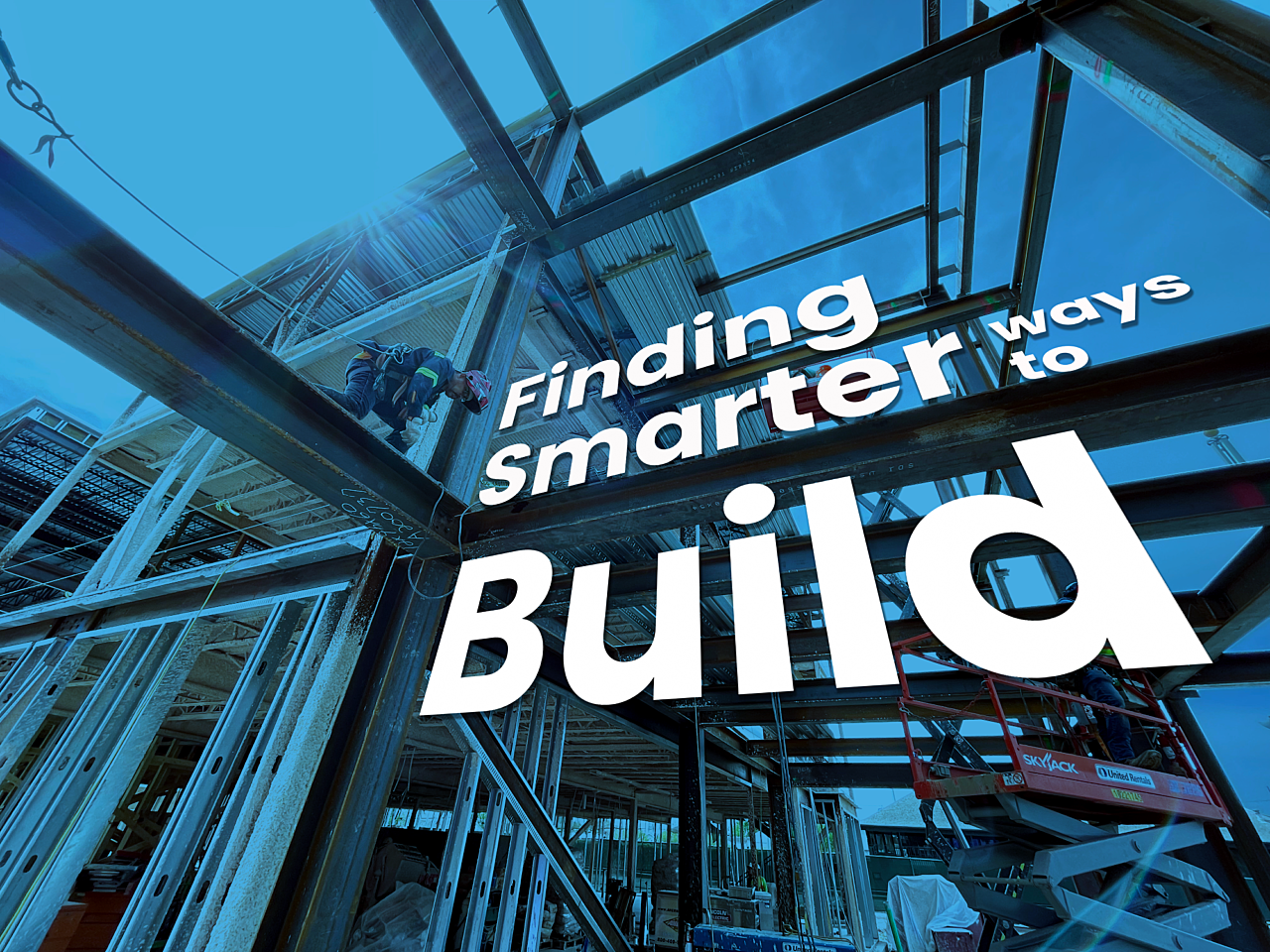
Desire for fast-tracked construction is becoming the norm, but it comes with its own set of challenges. From supply chain disruptions to labor shortages, there’s an increasing need to find smarter, more efficient ways to build. At the same time, new trends are shaping how projects are being delivered faster than ever. We’ve compiled our list of what’s driving fast-tracked construction—and some of the challenges that come with them.
Early Collaboration is Key to Speed
The old way of doing things—where architects design, then contractors build—just doesn’t work for fast-tracked project schedules. Instead, we see owners embracing more collaborative delivery models such as Design-Build (DB), Integrated Project Delivery (IPD), and Construction Manager at Risk (CMAR). The commonality in these methods is that each brings everyone – owner, architect, and contractor – to the table from the start. By involving contractors early in the design phase, teams can identify cost-saving opportunities, streamline procurement, and prevent design conflicts before delays occur.
Our team excels in CMAR/Design-Assist projects. In fact, we have completed or are currently working on more than 2.5 million square feet under design-assist delivery across 25 different projects in just the last five years. We work closely with design and trade partners early in the design process to identify as many cost saving options as possible. Our goal is to work proactively to develop the best design possible using the best materials available within an accurate budget.
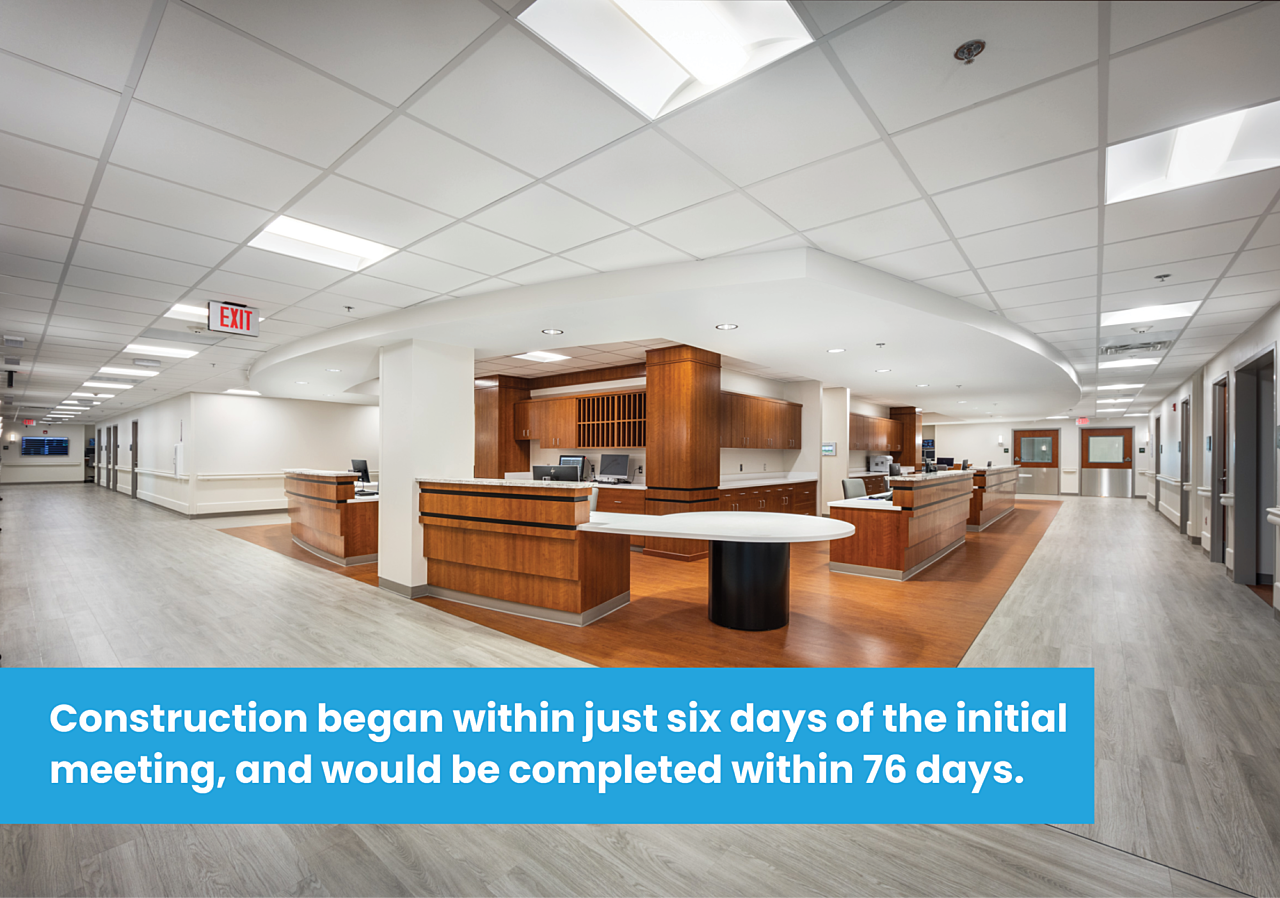
As the COVID-19 pandemic hit the South Louisiana area, Thibodaux Regional Health System contacted our team to build out 22,000 SF of shell space on the 3rd floor in the hospital to prepare for a possible surge in patients. The call came on a Thursday and our team walked the site the next day. A budget was approved that following Monday and our team would begin the buildout that Wednesday - just six days after the initial call. The project would be completed within just 76 days.
Prefabricated Construction Maintains ProgressMore and more, we are turning to prefabricated construction when appropriate to help meet tight deadlines. Instead of building everything on-site, key components—like patient room head walls for hospitals or structural elements for universities—can now be built off-site in a controlled environment. This means work can happen simultaneously both at the job site and offsite in a facility, drastically cutting down overall timelines. The benefit? Better quality control, reduced waste, a safe, controlled environment, and fewer weather-related delays. |
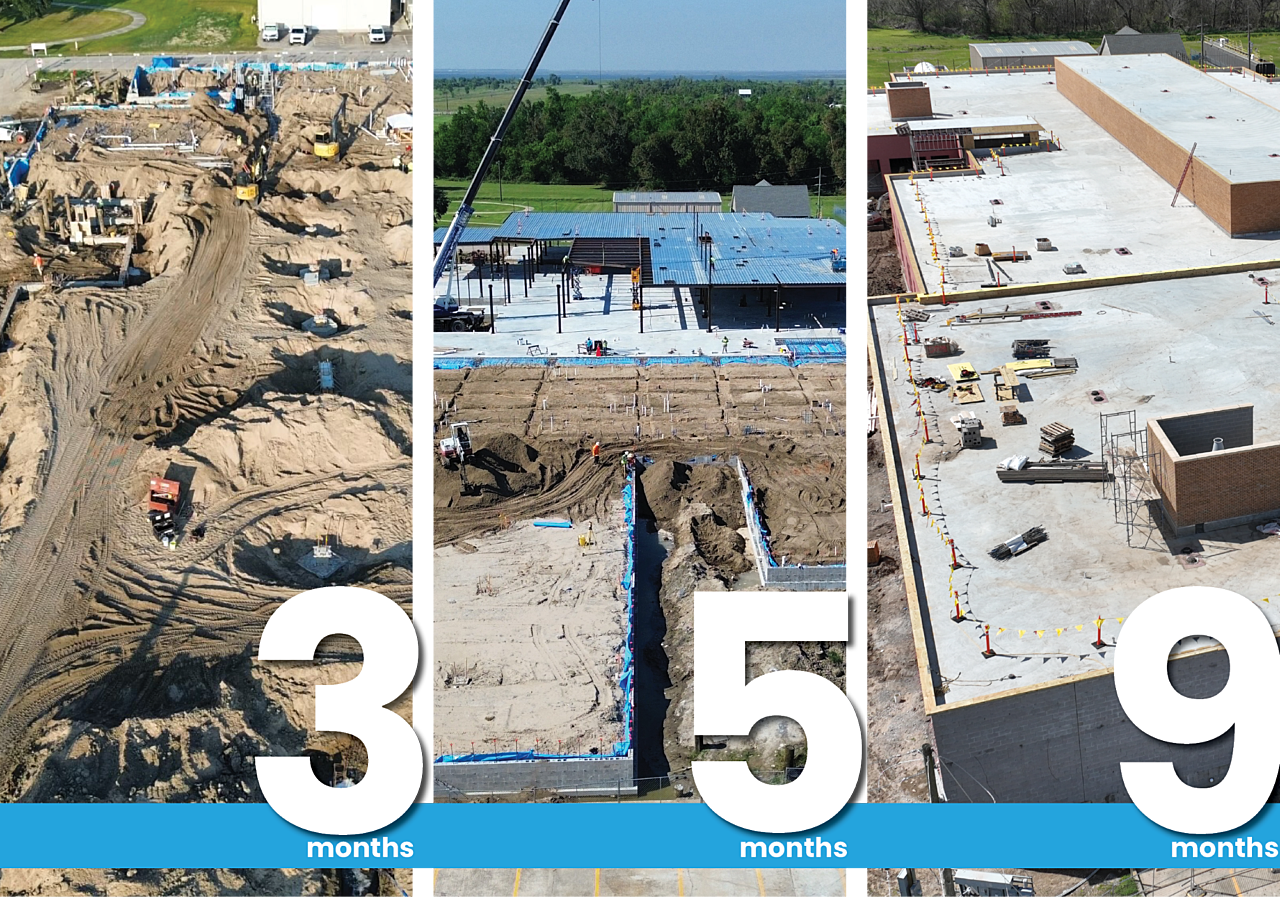
At Lady of the Sea General Hospital, for example, all underground plumbing and mechanical/electrical inwall systems were prefabricated and assembled off-site to allow for faster, more efficient installation on-site. This method played a critical role in enabling our team to build multiple portions of the building simultaneously. Pictured above is the project three, five, and nine months into construction. Prefabrication meant that steel structure could be erected on one end of the building while underground plumbing was simultaneously installed at the other. Within just nine months, the building was dried-in and preparing for build-out.
Technology Changes How We Collaborate
Technology is revolutionizing how construction projects are planned, coordinated, and executed, particularly when working under tight deadlines. One of the most powerful tools in this transformation is Building Information Modeling (BIM). BIM creates a highly detailed 3D digital representation of a project, allowing teams to visualize every aspect of the build before construction even begins. This proactive approach helps detect clashes between structural, mechanical, electrical, and plumbing systems early in the process, preventing costly rework and delays.
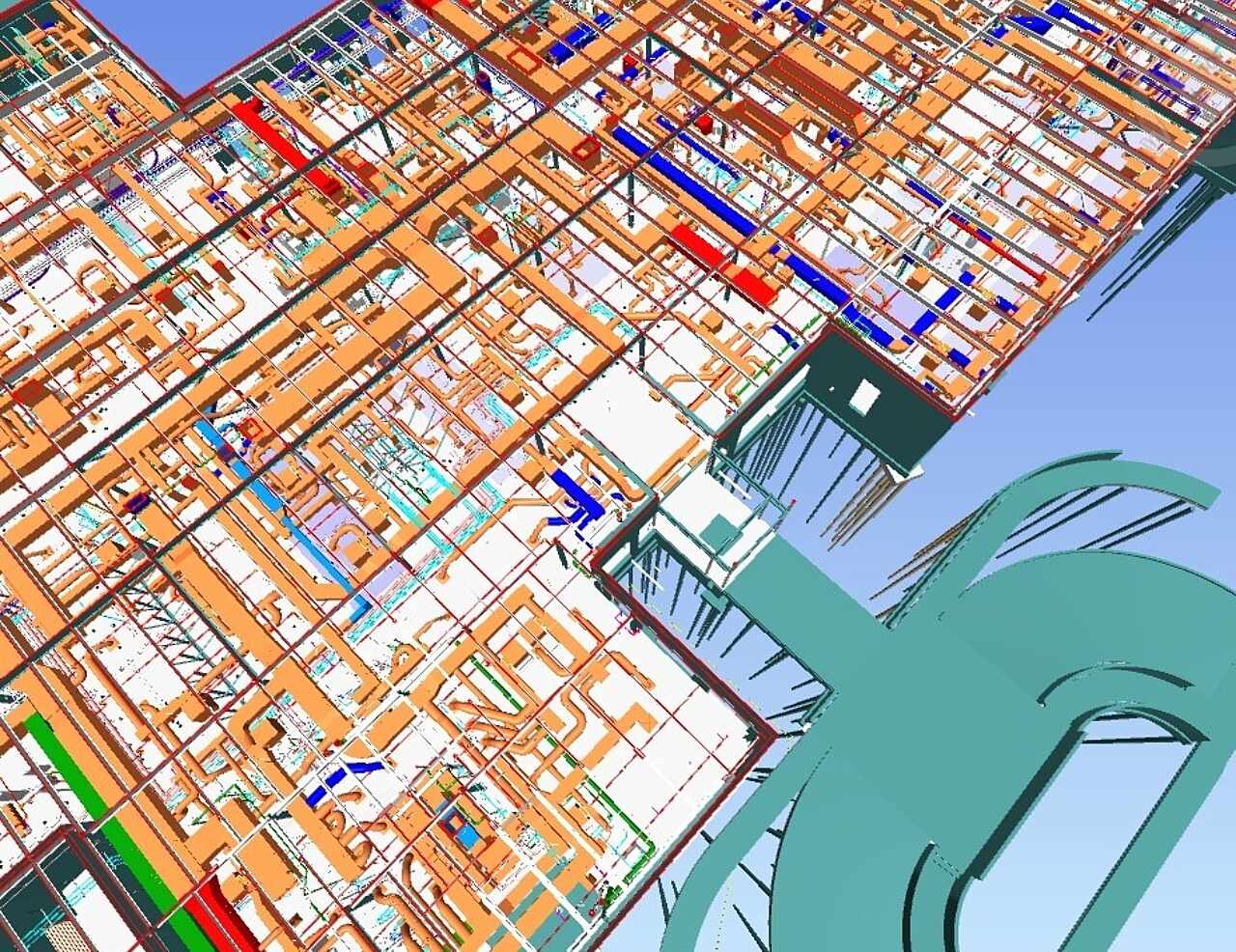

Our team is also utilizing OpenSpace (above), an AI-driven spatial software that allows us to document construction and provide clear visual conditions of the site and building in real time. This information is shared with the team during construction to document progress and is provided to the owner at the end of the project. When complete, the owner has a visual record of the location of every major system within the building for future renovations or expansions.
As fast-tracked projects push traditional construction methods to their limits, BIM and other AI software have become an essential tool for mitigating risk, maintaining accuracy, and ensuring efficiency from design through completion.
Meeting Aggressive Timelines During Construction
Delivering fast-track projects requires having the right team in place from the start. Daily communication during operations is key with all team members - from owner and designer to contractor and trade partners - having full buy-in of the project's schedule.
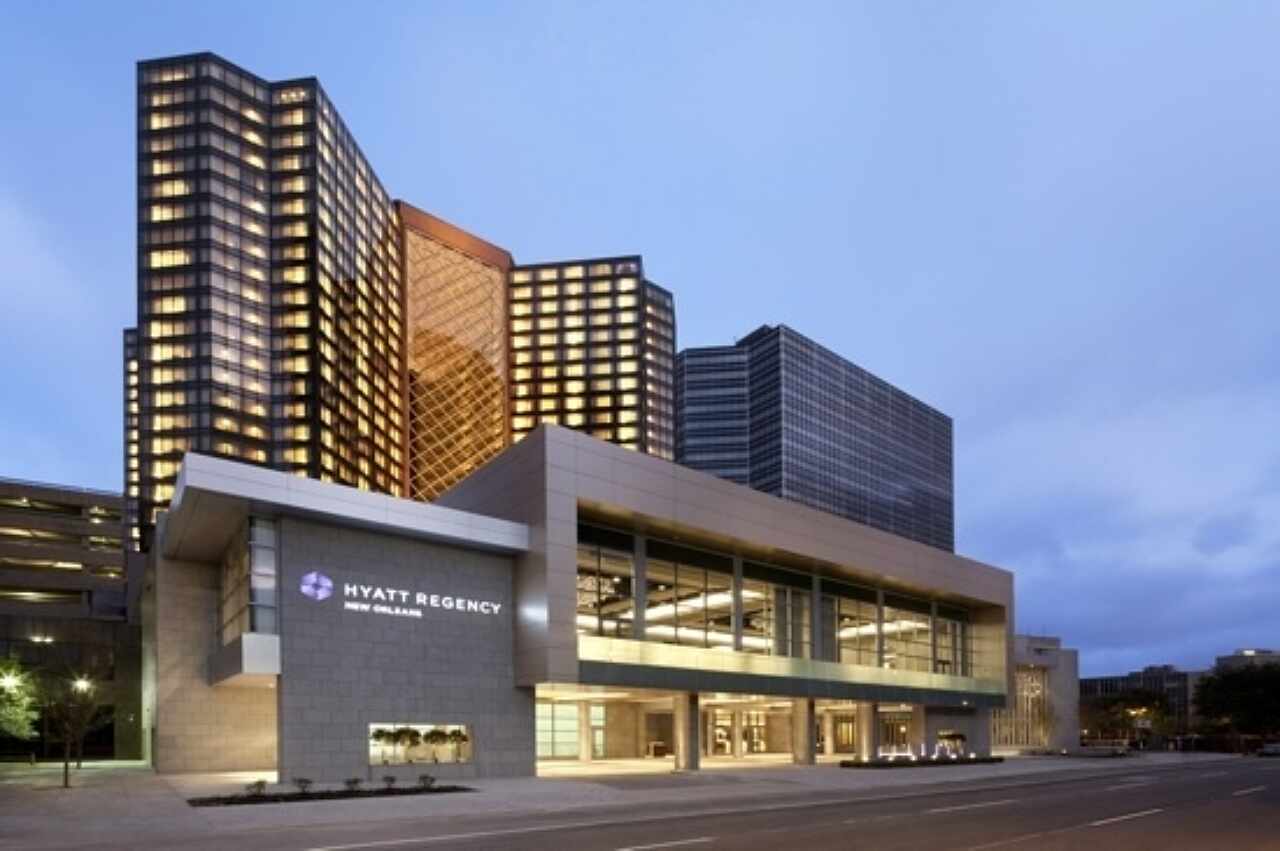
In order to achieve the Hyatt Regency's aggressive 14-month schedule, all areas of the facility required work to initiate on day one. The project team and subcontractors worked in shifts so work would continue 24 hours per day. The entire electrical, life safety, and conveying system, and a majority of the mechanical systems were replaced and/or redesigned to modern codes in the entire 1.2 million-square-foot facility. Electrical gear arriving within four weeks of the Notice to Proceed was instrumental in the project’s success.
Navigating Supply Chain Challenges to Mitigate Delays
We know that supply chain disruptions can completely derail a fast-tracked project. Long lead times on critical materials like steel, electrical components, and HVAC systems make it harder to stick to tight schedules. To stay ahead, our team consistently refines its procurement strategies, locking in materials early, and sourcing alternatives when necessary.
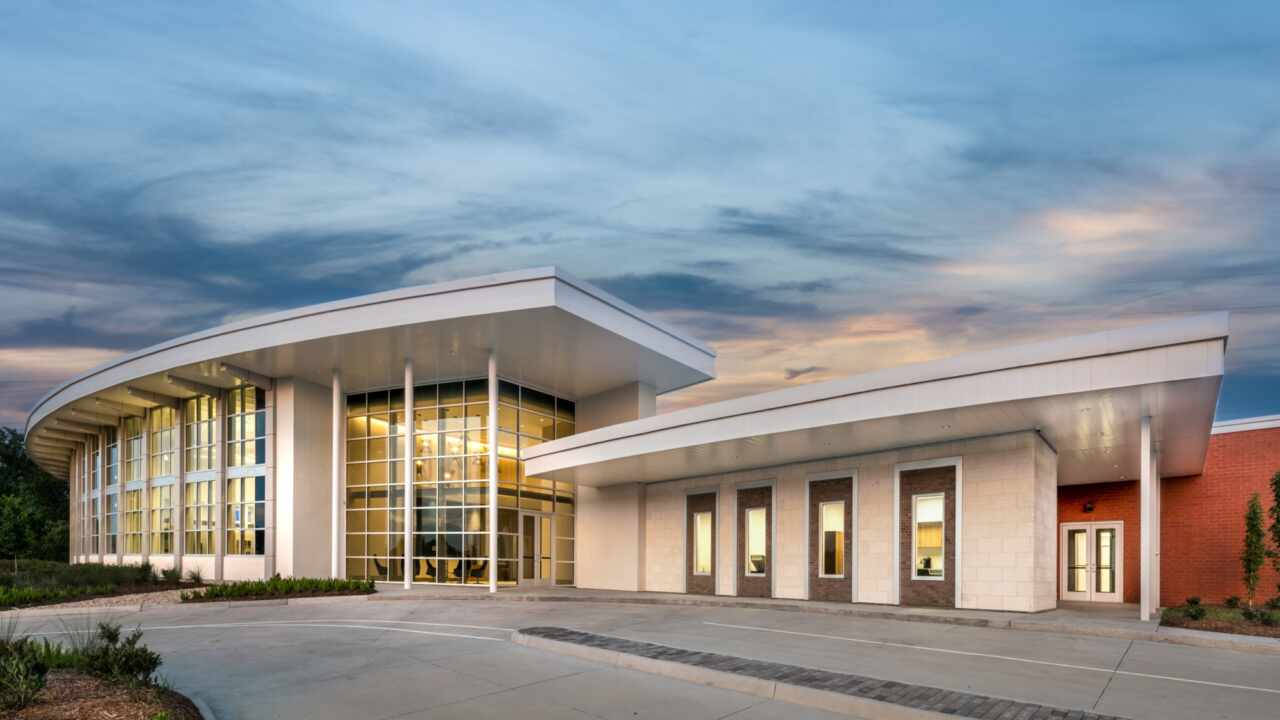
For example, at the recently completed Wellness Center at Bayou Bend, we worked closely with the owner and architect to lock in steel pricing as well as mechanical equipment pricing early in the design phase. All this during the post-COVID supply chain challenges. This decision would ultimately save nearly $500,000 on the overall project budget and allow for an on-time delivery.
Balancing Speed to Market with Quality and Safety
Rushing a project can lead to mistakes, safety issues, and subpar workmanship. When schedules are compressed, there’s a higher risk of coordination errors, missed details, and increased stress on workers. During construction, we follow a project-specific three-phased quality control plan. Before every major milestone, we define requirements for all products, materials, craftsmanship, and performance. We identify any issues as soon as possible, adding any unsatisfactory work to a working punchlist. During final inspections and testing, we ensure compliance with our initial quality standards. These steps ensure that building quality is set from the beginning and carried throughout the project while holding all team members accountable.
Fast-tracked construction is here to stay. As demand for quicker project delivery continues to grow, we continue to push the envelope—adopting new technologies, refining our processes, and strengthening collaboration across our already broad partner network. Our ability to adapt to the speed of change while maintaining quality keeps us in the forefront as industry leaders.
Noteworthy Projects & Recent Completions
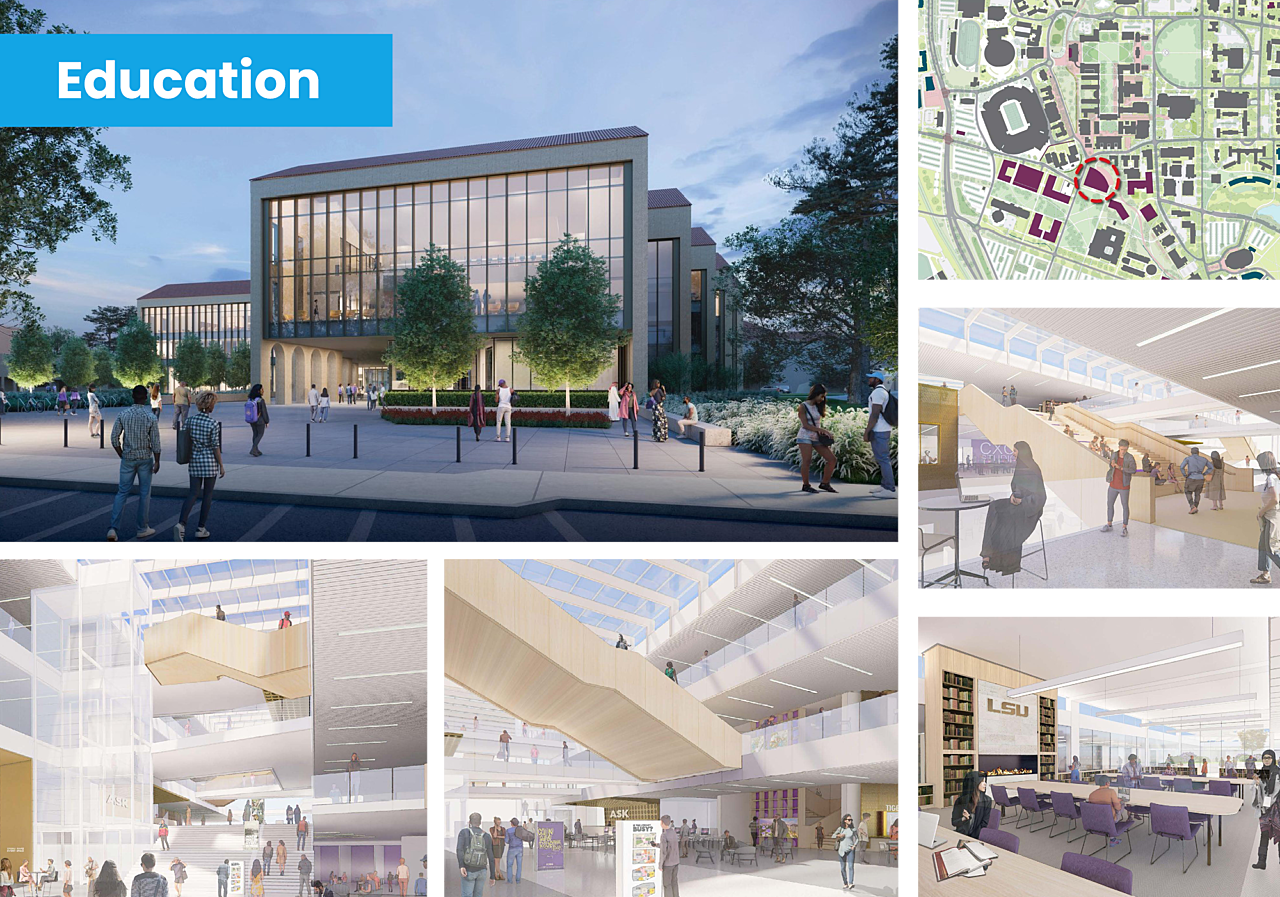
LSU Learning Commons
In collaboration with our JV Partner, Milton J. Womack, the Womack-Donahue team was selected to serve as the CMAR for this momentous project on LSU’s campus. The new nearly 200,000-square-foot state-of-the-art library will be centrally located on the campus, uniting the LSU community in ways and methods not possible in the current main library, serving as a bustling hub of classrooms, flexible event spaces, study spaces, collections, exhibit spaces, staff and partner spaces, and technologically-rich creative spaces. This $150 million project will undergo a lengthy preconstruction process with construction expected to begin in Q3 2026.
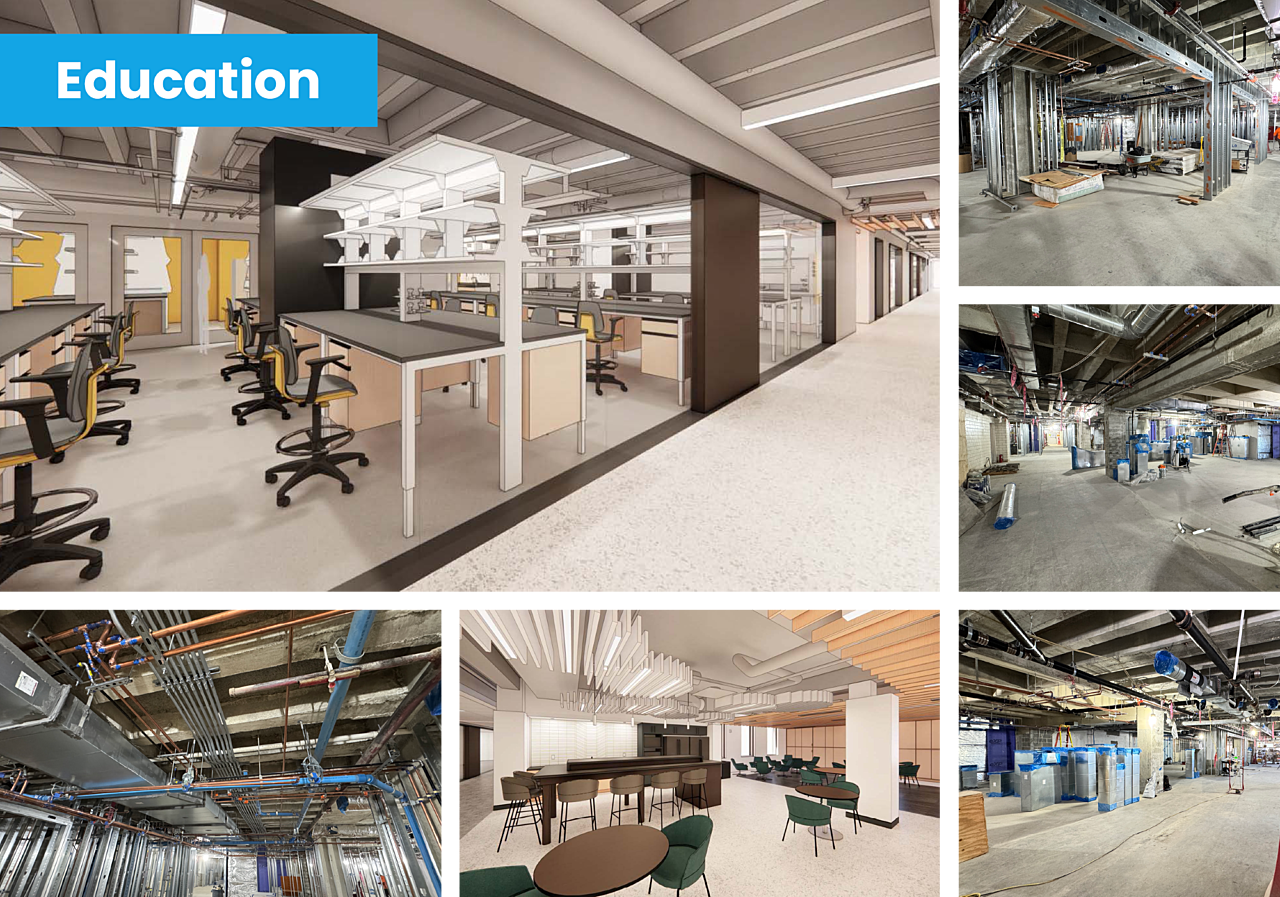
Tulane Hutchinson 7th Floor
Progress continues at Tulane University School of Medicine’s 7th Floor Laboratory renovation. Overhead MEPs over the laboratory spaces and inwall MEPs are nearing completion. In many areas, drywall installation has begun with flow across the entire space. Finishes will begin in several areas in the coming weeks. We’re looking forward to the finishes and trim out phases or this project.
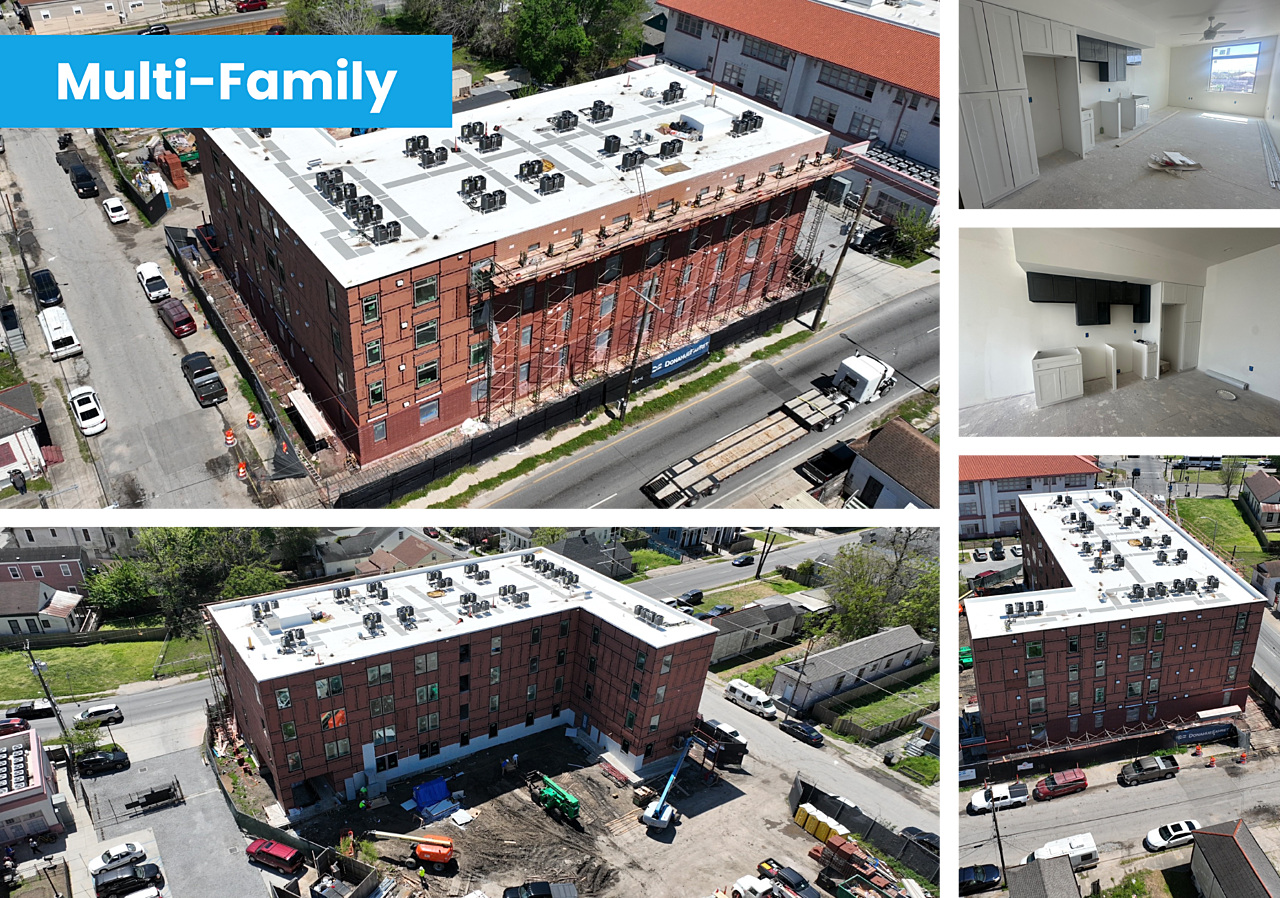
Arts Apartments
Scheduled for completion in early June, Arts Apartments will provide 40 mixed-income housing units across four floors. Currently, our team is working on interior finishes, flooring, and trim.
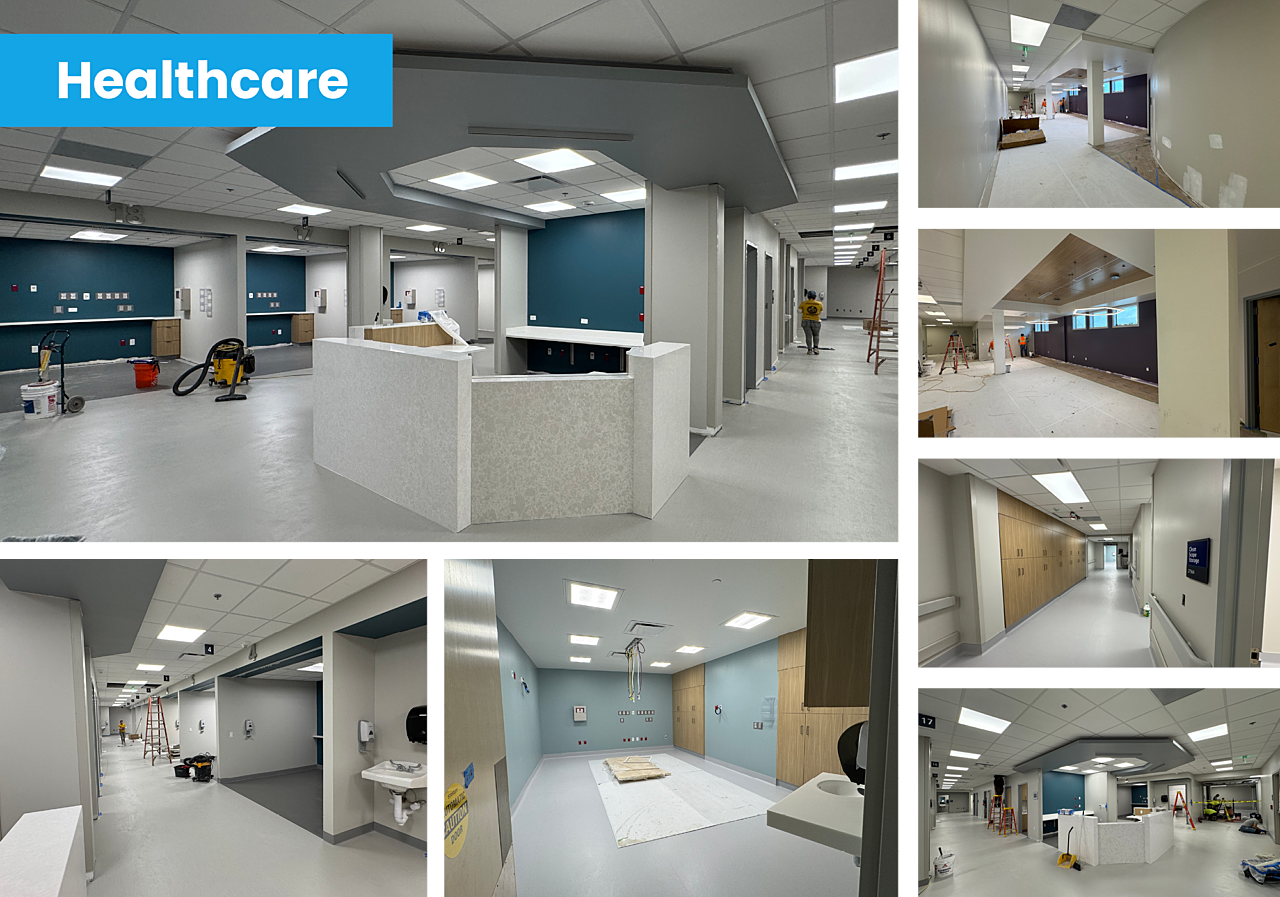
Slidell Memorial Hospital Phase II
Fresh off the heals of the recently completed Phase 1 addition, our team is nearing the end of this Phase 2 renovation to Slidell Memorial Hospital. Located on the 2nd floor of the existing facility, this 13,000 square foot renovation will connect directly to the Phase 1 addition. It will provide three endoscopy surgery rooms, 17 post-operation bays, a nurses' station, and a chapel. We are currently on track for completion this spring.
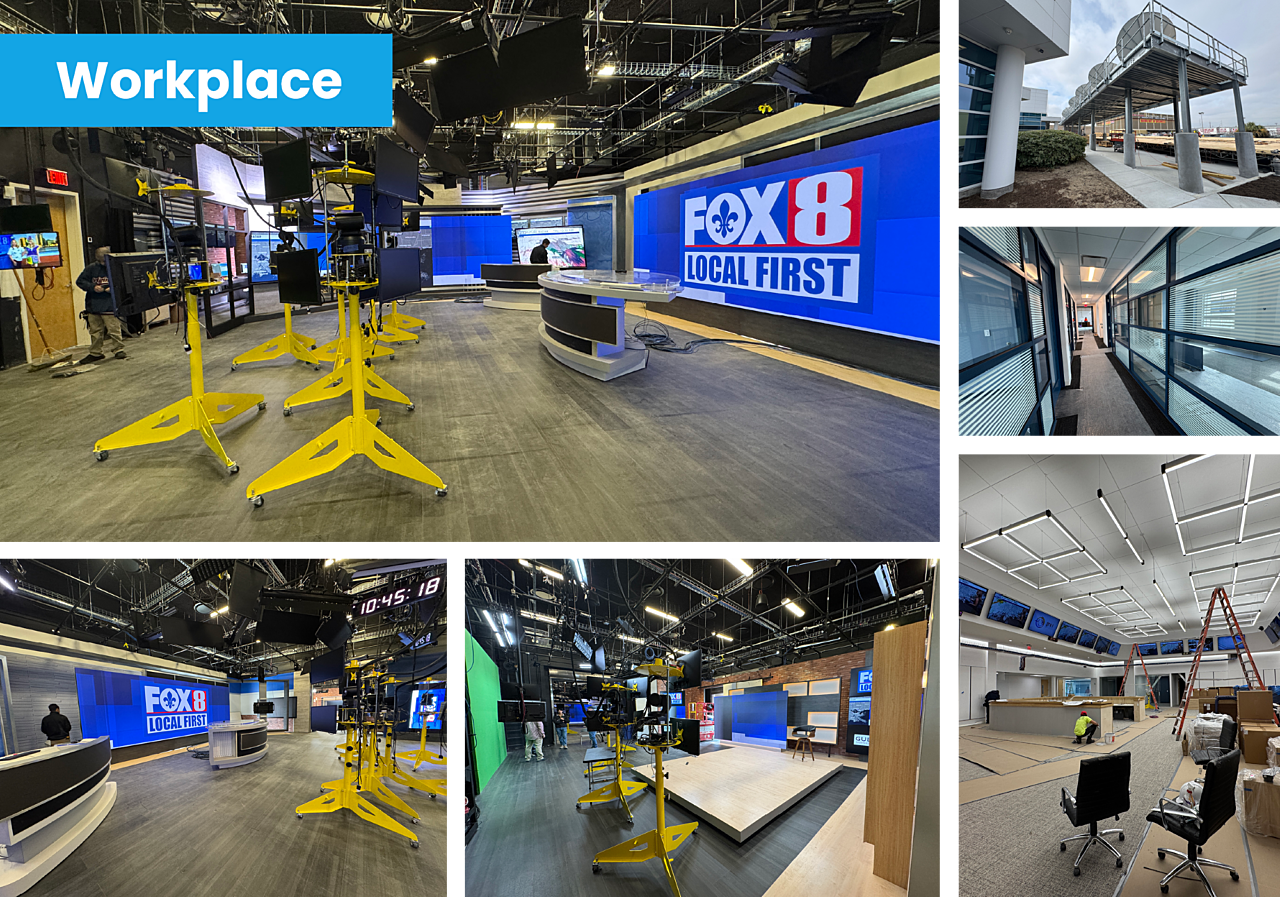
WVUE Fox8
The former headquarters of Pontchartrain Housing Corporation has been transformed into a redesigned 37,000-square-foot studio and office space for WVUE Fox8 News. The first floor became a state-of-the-art newsroom and two new studio areas dedicated to breaking news, investigative reporting, and sports. The second, third, and fourth floors have been refurbished, with the installation of new flooring and carpet, and the removal of select partition walls to create more spacious office areas. Externally, a new steel structure supports six ground-level satellites and provide ten covered parking spaces.
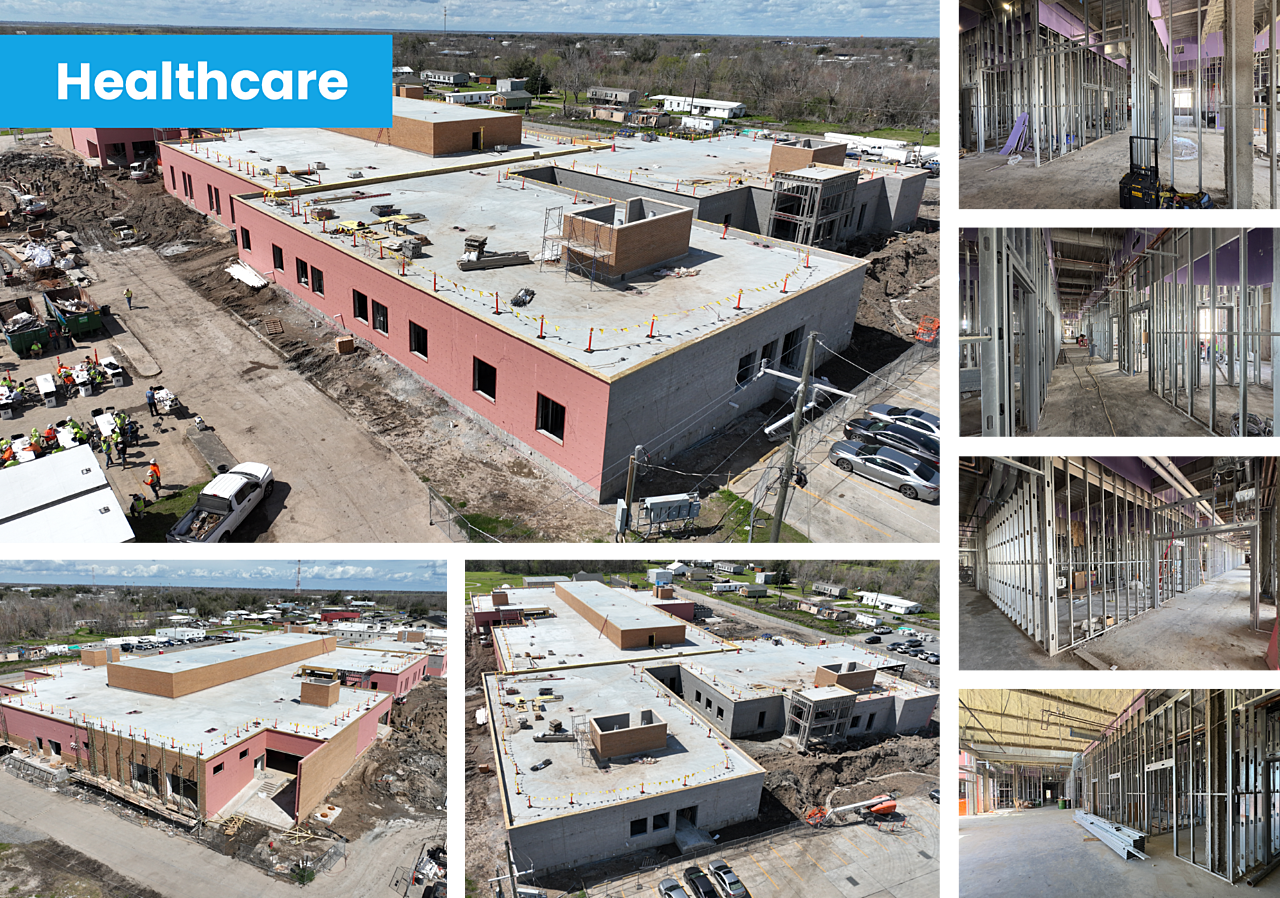
Lady of the Sea General Hospital
Our team is making great progress at Lady of the Sea General Hospital. On the exterior, waterproofing and the brick facade are nearly complete. The first of the three horseshoe entrance drives have been poured with the main entrance underway. Inside the building, MEP overhead and inwall rough-ins are nearly 60% complete with finishes to follow. The project is scheduled for an early winter completion.
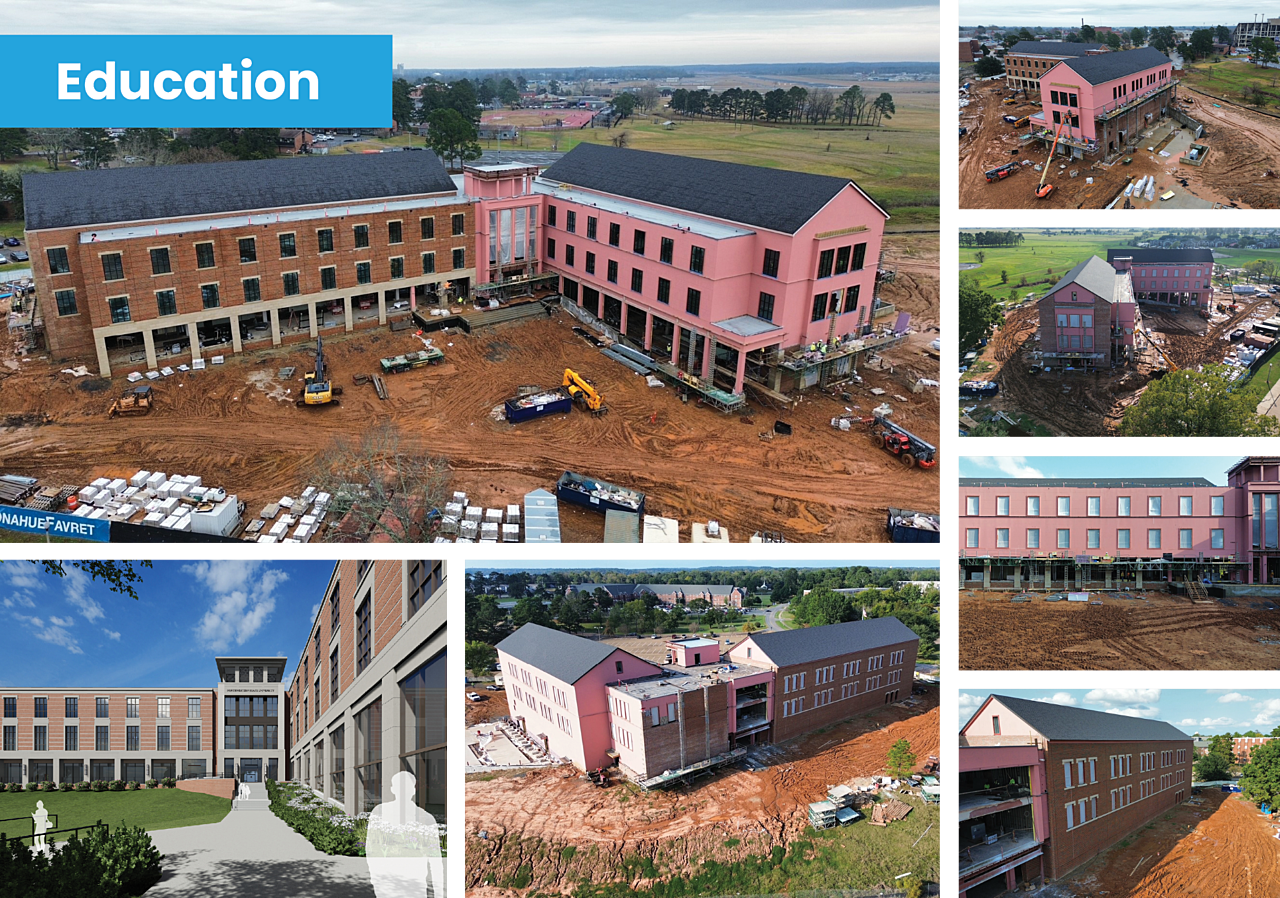
Northwestern State University Alost (Kyser) Hall
This project consists of demolition of Caddo Hall and the construction of new 72,000 SF multi-story classroom and administrative building at Northwestern State University. The building will consist of multi-purpose classrooms, teaching labs, simulation clinics, administrative offices, student collaboration spaces, and support areas. The pre-existing building on site, Caddo Hall, has been demolished. The project is currently under construction after our Preconstruction Team established the project’s GMP, having successfully navigated through current inflation issues, delivery challenges, and labor shortages.
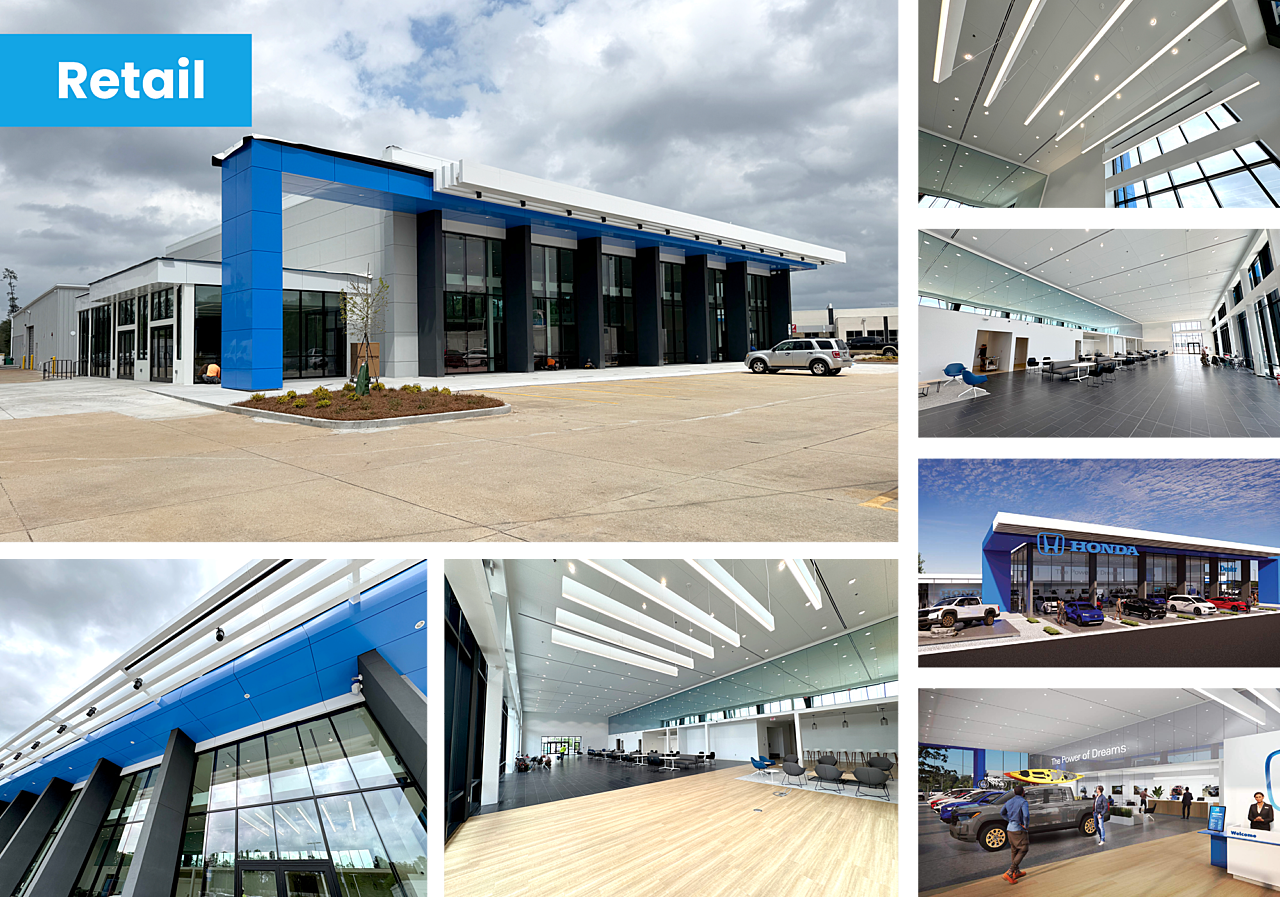
Honda of Covington
Renovation of the Honda of Covington automotive dealership is nearly complete. This project will deliver 16,300 square feet of renovated and additional space. Renovations include new storefront and curtain wall glass facade, and newly branded front entry feature. The showroom is being completely renovated to an open-air concept featuring 22-foot high ceiling height, new LVT and ceramic tile floors, Carvart glass wall with signage, and remodeled bathrooms. Our team is on schedule for completion this spring.
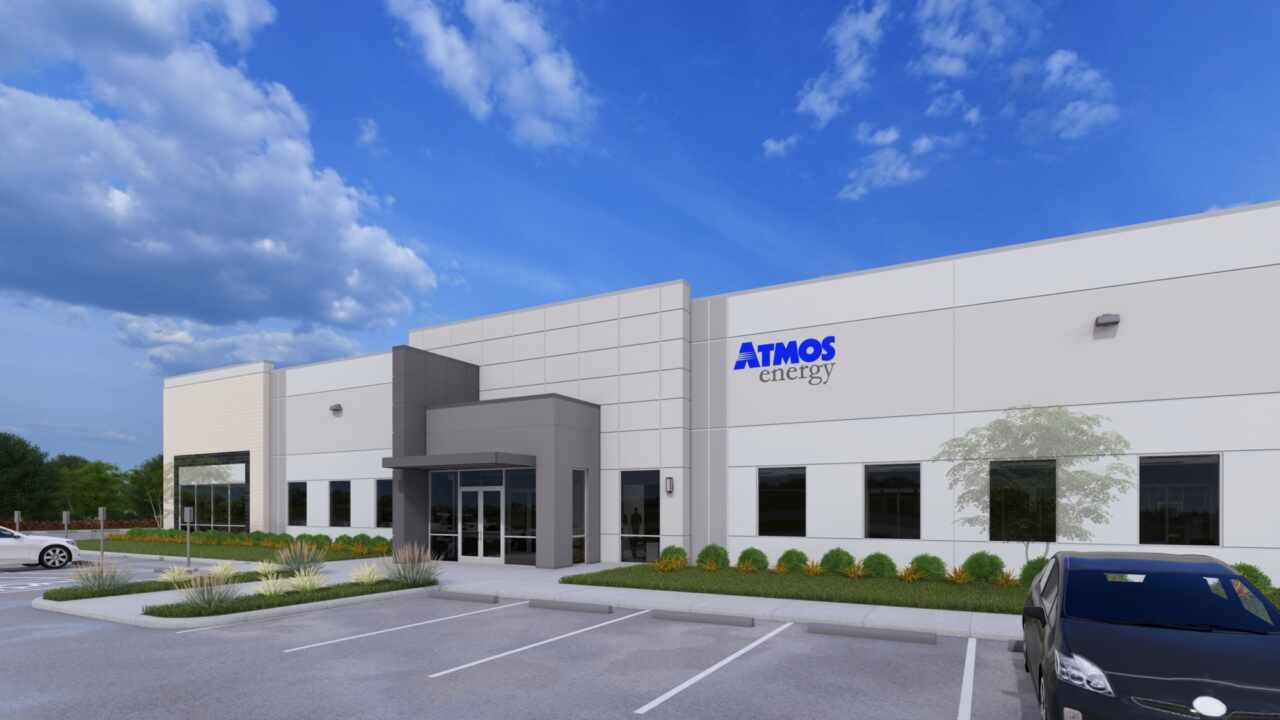
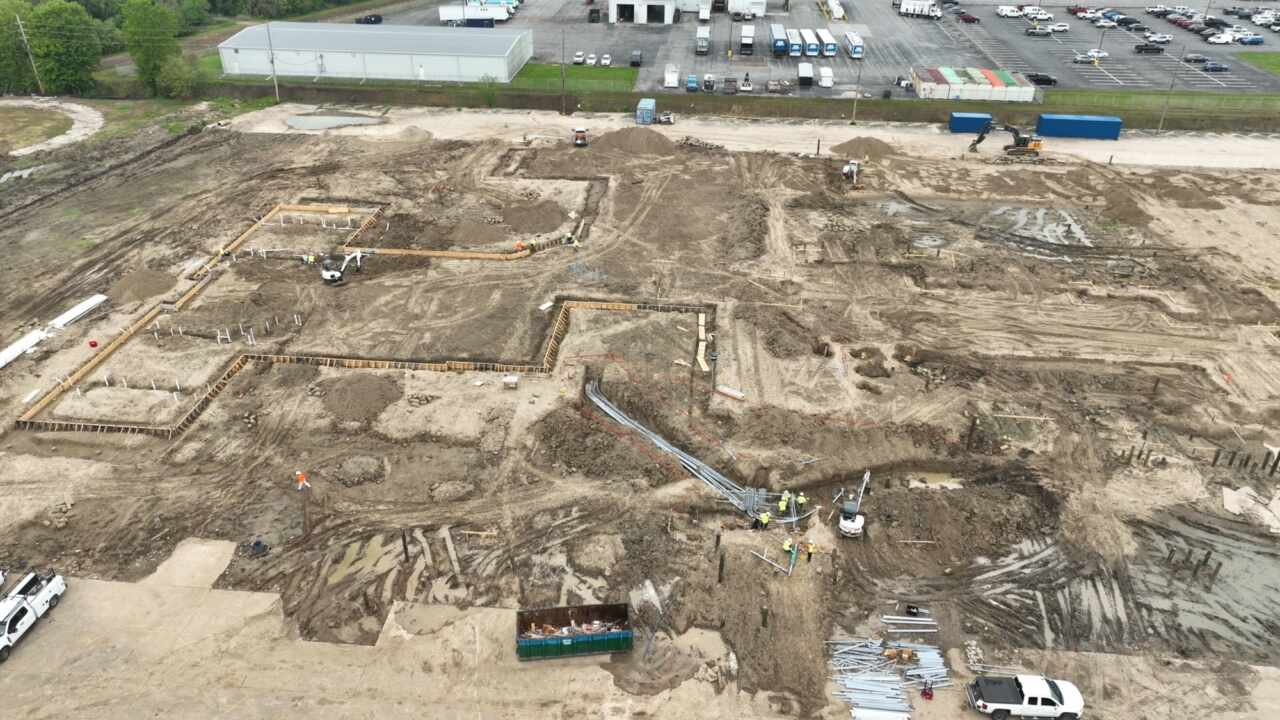
Atmos Energy
Our team is in the early stages of construction for the new 30,000-square-foot Atmos Energy corporate office. Site utilities have been installed and the building's foundation is complete. Situated on timber piles, the slab will be poured in the coming weeks with tilt wall and steel erection to follow. This project is scheduled for a fourth quarter completion.
CommCare Stassi
With the site of the former Louisiana Technical College now cleared, we've begun construction of this new 74,600-square-foot skilled nursing facility. The new ground-up facility will feature 133 beds across six residential wings and a central core building. The exterior will blend a Hardie and brick façade on a wood-framed structure.
Awards & Recognition
DonahueFavret earned the highest award of distinction from ABC National this year. Our work on the Tulane Reily 4th Floor Renovation received a National Excellence in Construction Eagle Award. Special thanks to our client, Tulane University School of Medicine, and design and trade partners for their collaboration throughout the project.
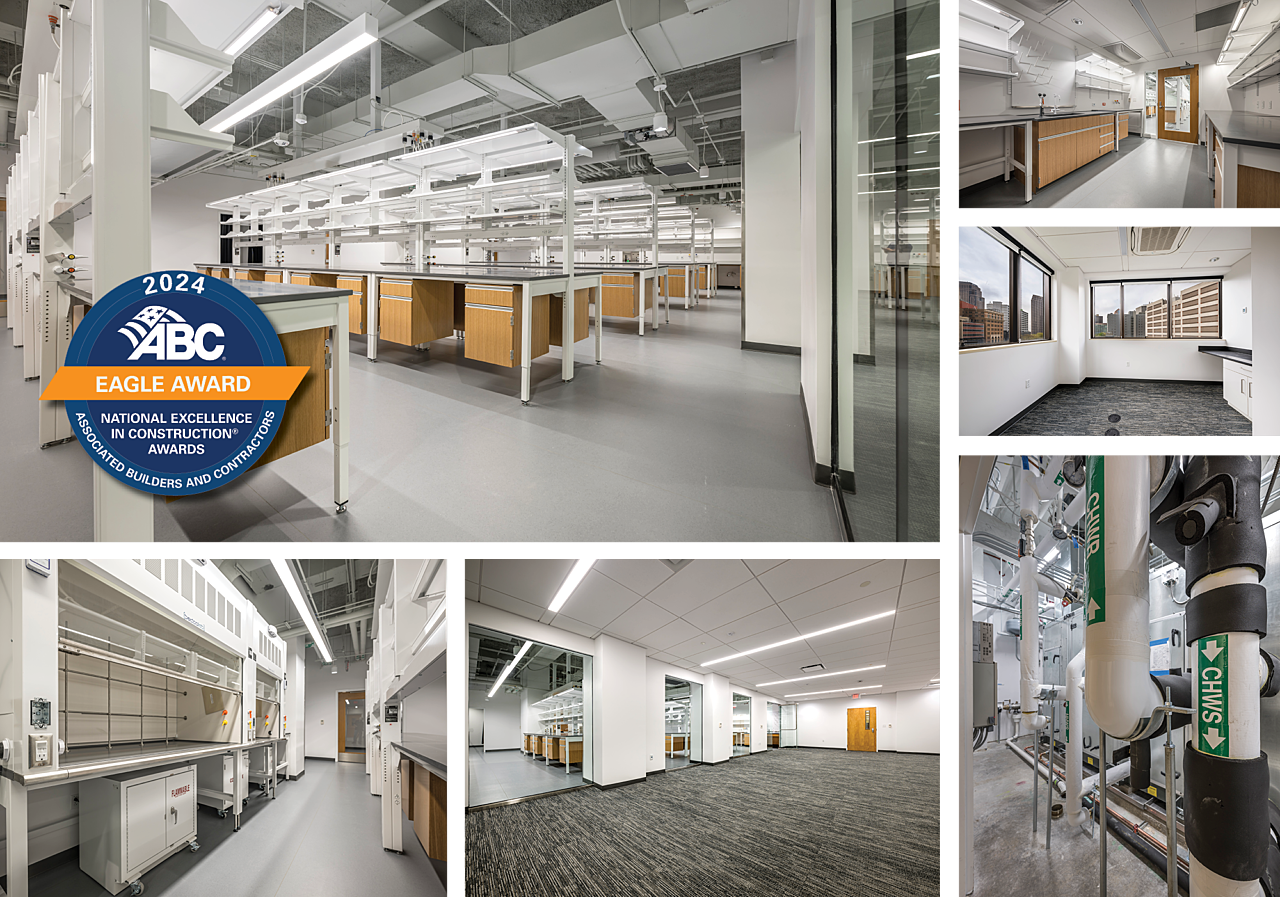
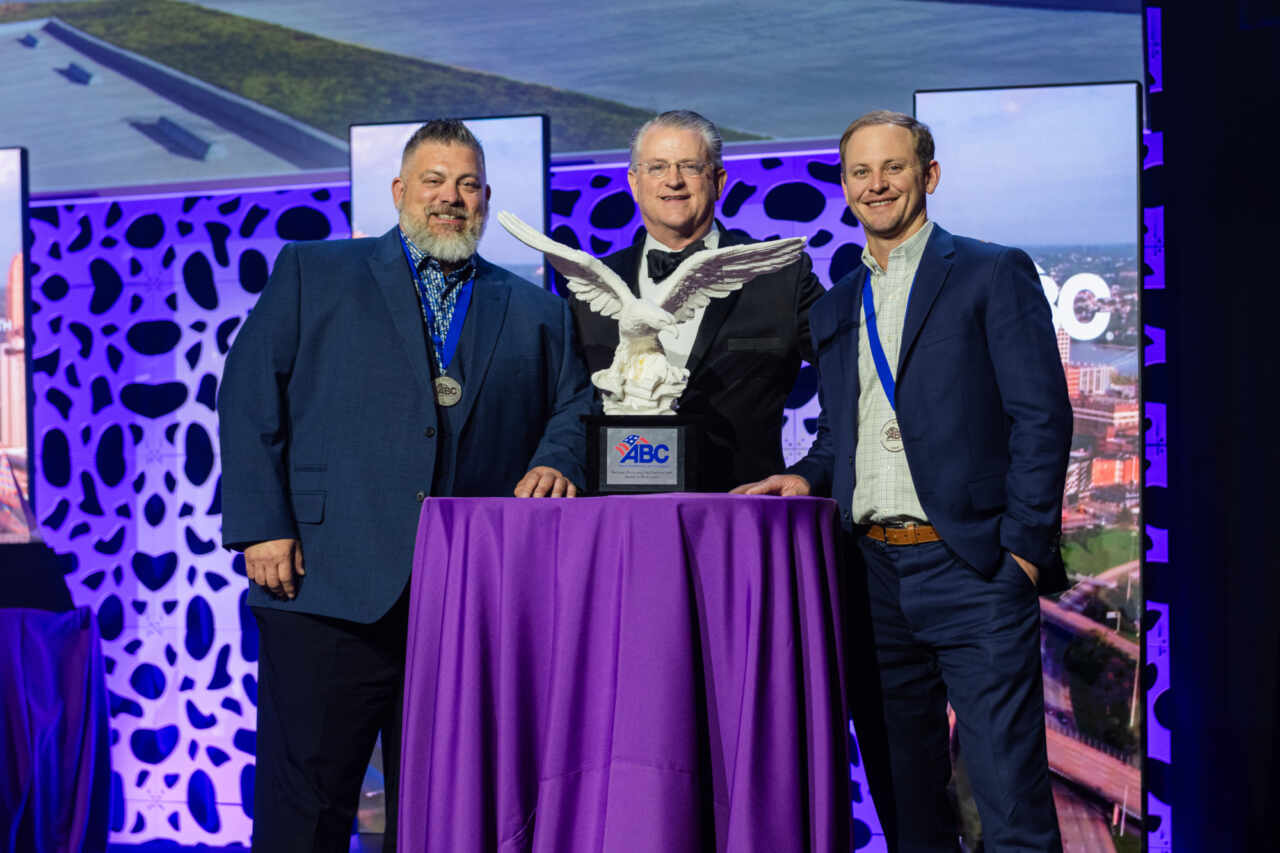
We’re excited to support our own Sr. Project Manager, Bill Mardis, on his latest venture as Chairman of the Board for the ABC New Orleans/Bayou Chapter. He was sworn in on Jan. 16th and shared with us his goals for the upcoming term. His primary goal is aimed at increasing membership of the chapter, as well as increasing STEP participation from member companies.
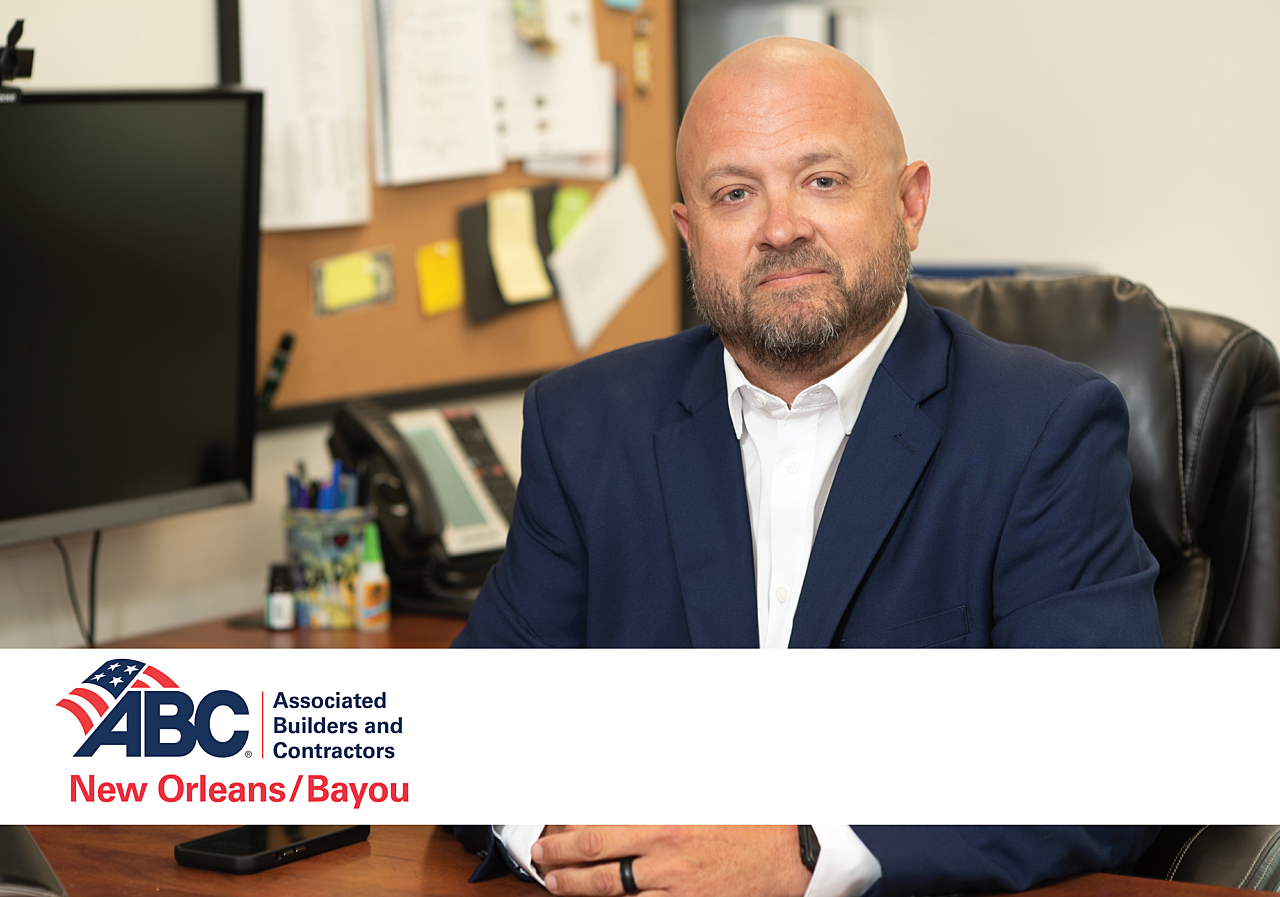
Upcoming Events
Mark your calendars! Save the date! We’re thrilled to announce that our fifth annual #DrivingFORECharity golf tournament is set once again for this fall. More details and sponsorship opportunities coming soon
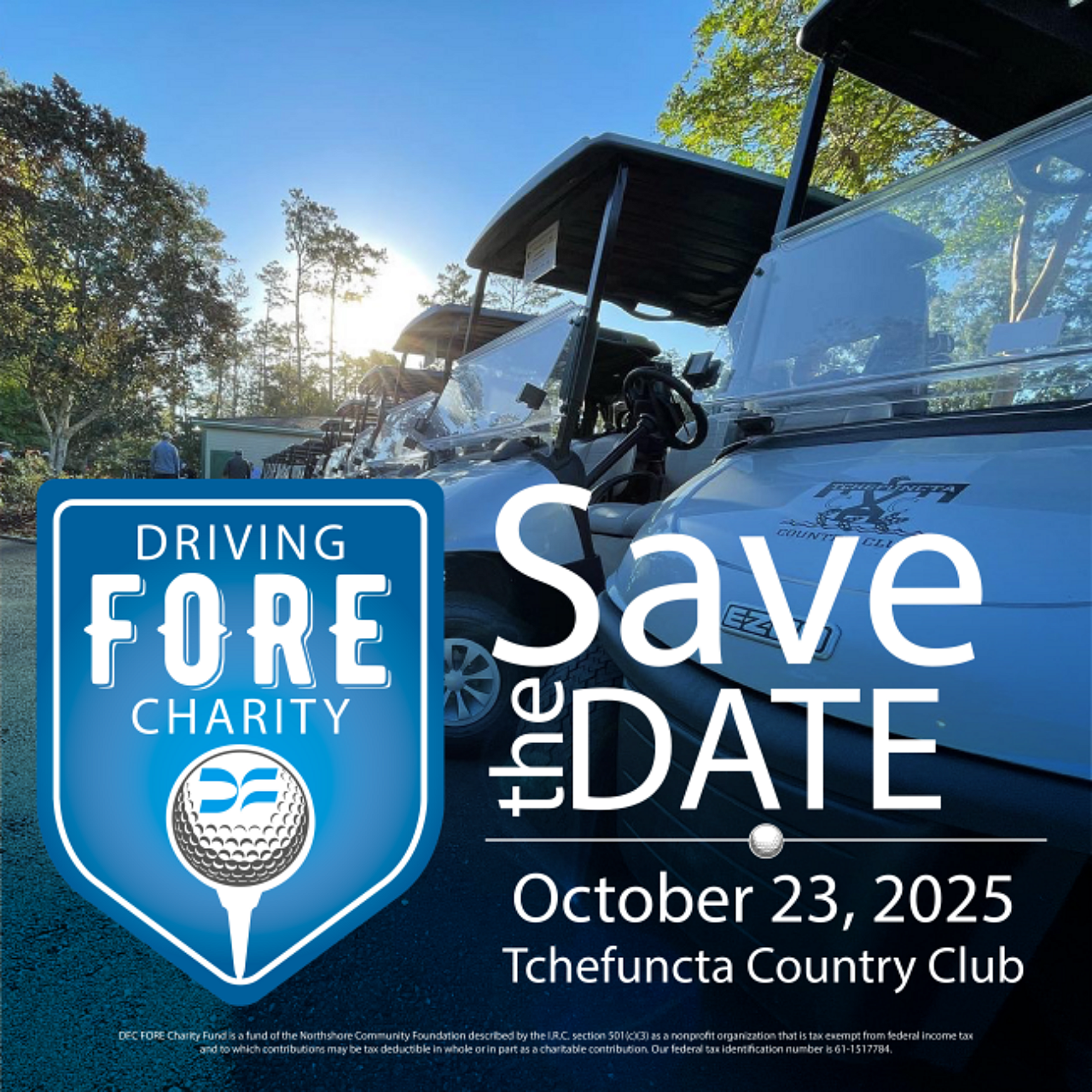