Heavy BIM coordination mitigates project challenges.
DonahueFavret Contractors was selected to construct this state-of the-art 66,000 SF corporate headquarters for Globalstar Technologies based on GCs and Fee along with a client interview. Once selected, our Preconstruction department immediately began working with the architect and engineers on selecting exterior skin systems, MEP systems and site analysis all while constantly monitoring the overall construction budget. Our team was released to start site work and clearing on an early release package while the design progressed. This project utilized BIM coordination for the entire Preconstruction efforts including all MEP systems, curtainwall, structural steel and modular walls.
Once the design was complete, our team, which had been in nearly all of the Preconstruction meetings, made a seamless integration into the construction phase. The project consisted of deep foundations, structural steel structure, curtain-wall glazing system, metal panels, high end interior finishes and interior modular walls. Due to the high level BIM coordination, the project came together with minimal questions or challenges.
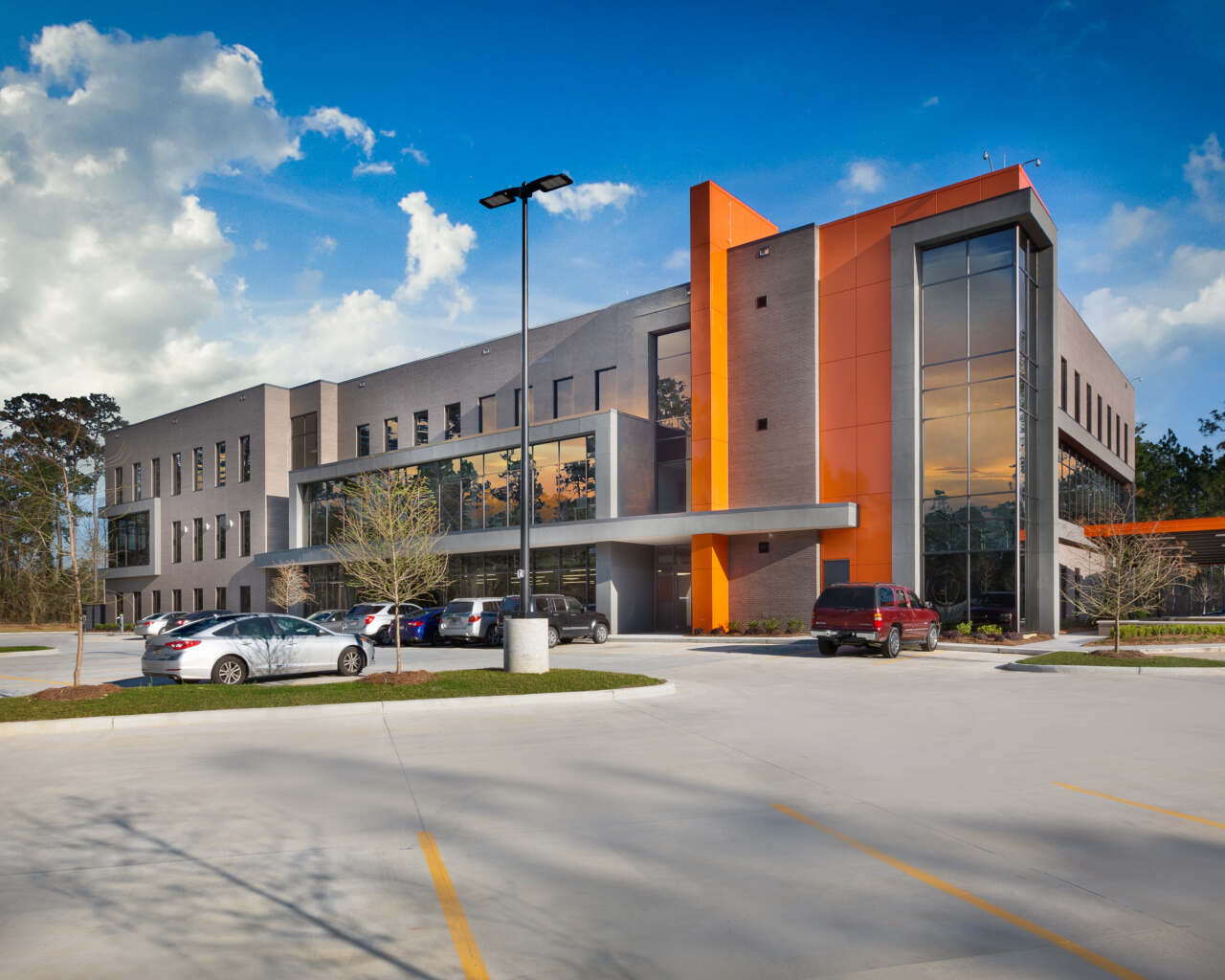
Square Footage
66,000 SF
Completion
13 months (2018)
Owner
Thermo Covington, LLC
Architect
Project Location
Covington, LA
Collaborative success.
From the outset, our project team embraced the use of BIM technology to streamline the schedule and ensure we stayed on budget throughout the entire process. This approach made coordination between all stakeholders efficient, enabling us to make real-time adjustments when needed. Open lines of communication and a shared vision allowed our team to address challenges promptly, finding creative solutions that aligned with the project’s objectives. The success of this project was a testament to the synergy between cutting-edge technology, forward-thinking solutions, and a highly collaborative design team.

Advanced quality control and collaborative BIM coordination.
Quality Control was documented and administered with much more than the traditional methods of simple observation and citation. The project was modeled and coordinated in BIM for 100% structural, architectural, mechanical, electrical, sprinkler, and plumbing systems. Our team hosted weekly BIM coordination meetings during the design-assist preconstruction phase that promoted participation with all parties. This resulted in zero significant field conflicts and no change order request for space planning or coordination of the extensive modular wall scope.
An envelope consulting engineer was brought onto the project early to assist in the design of curtain walls and exterior systems. Meetings were held with all subcontractors to discuss the interaction of dissimilar materials and unique conditions. Upon installation, the consulting engineer was also involved in the inspections of all exterior systems.
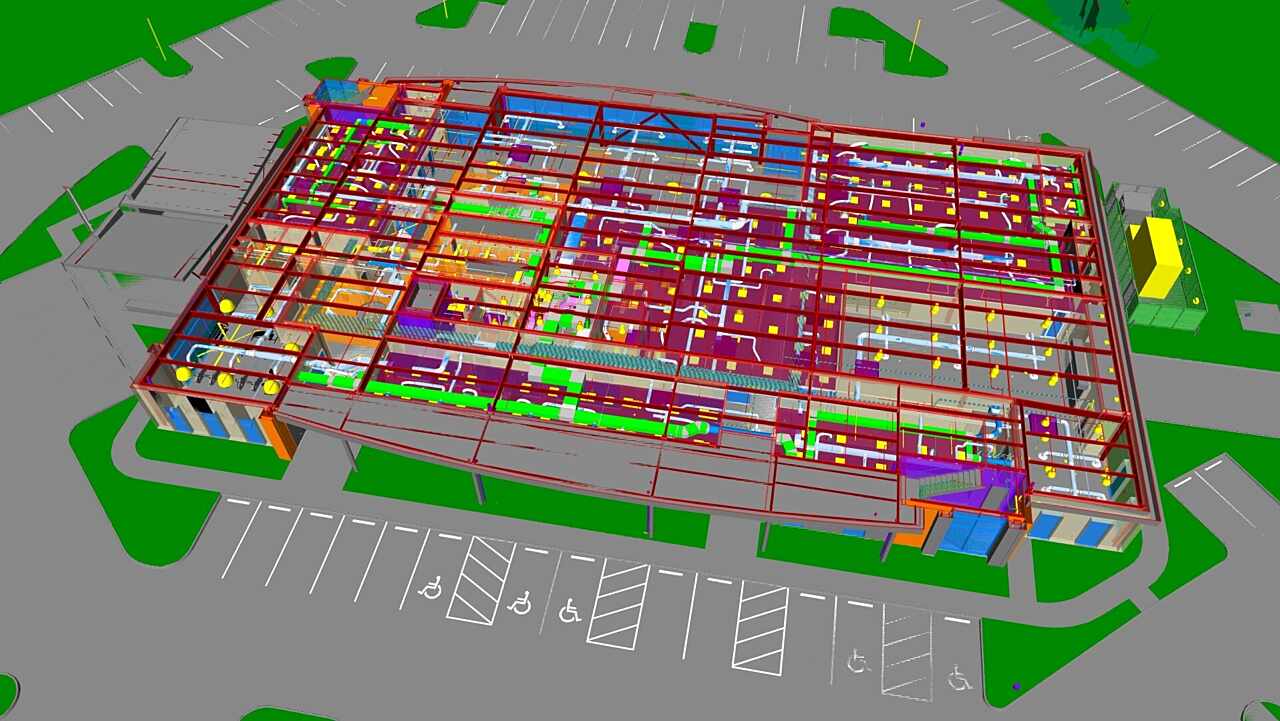
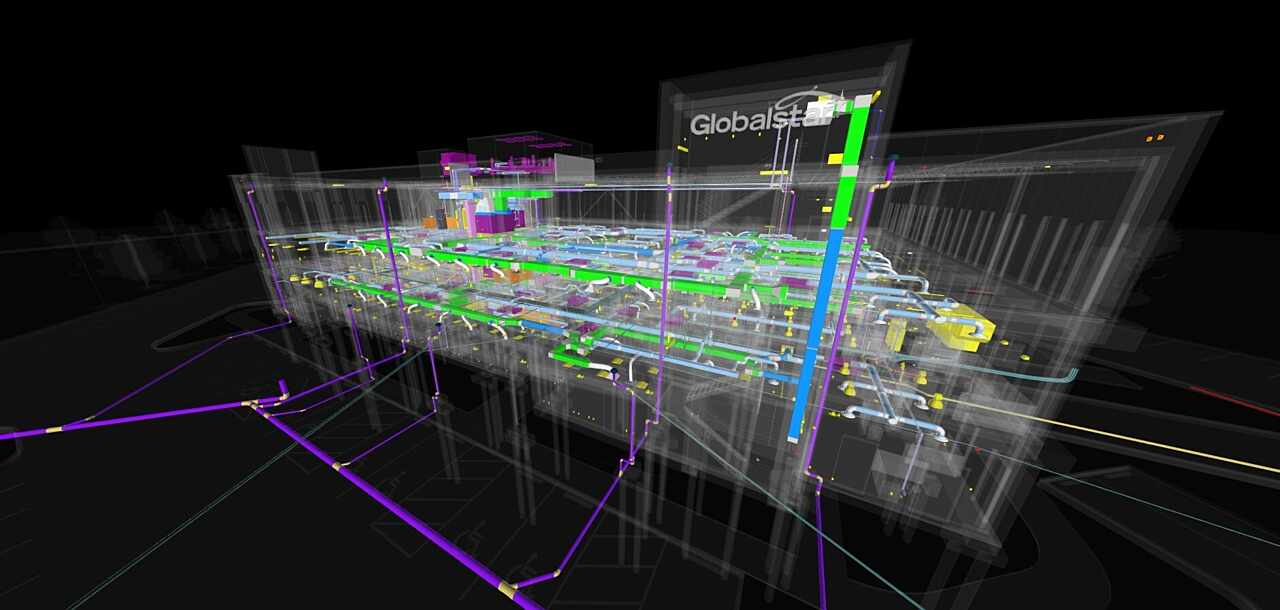
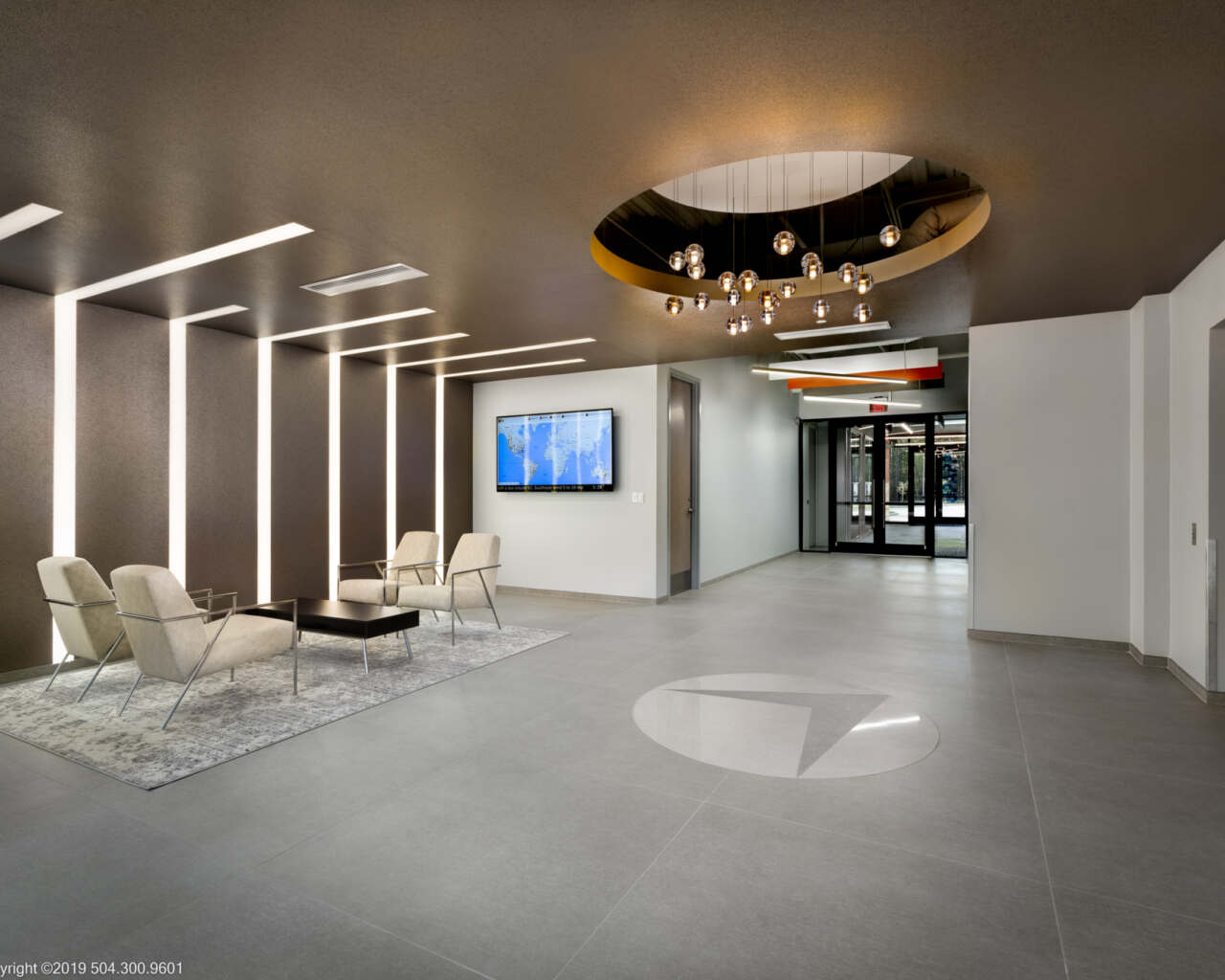
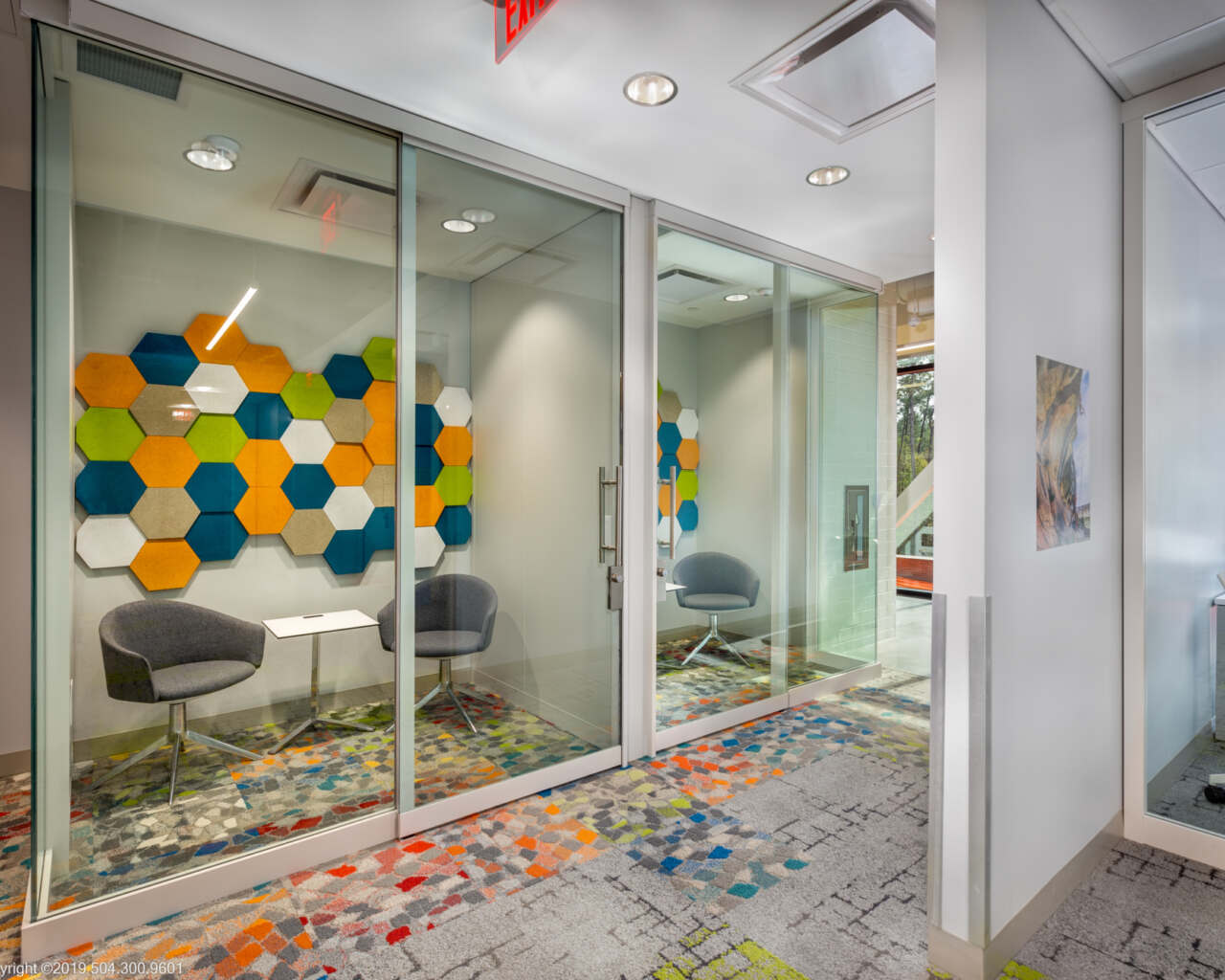
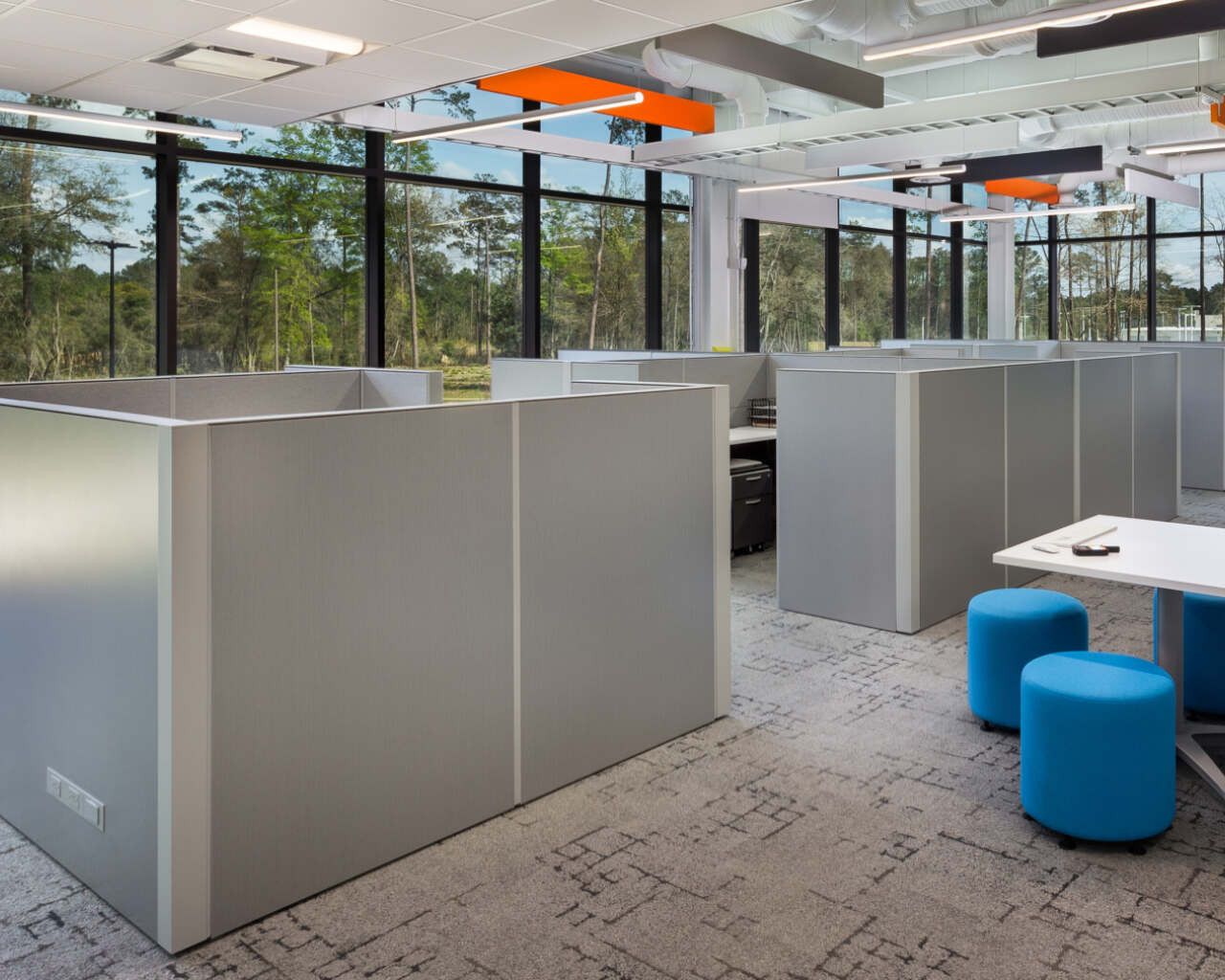
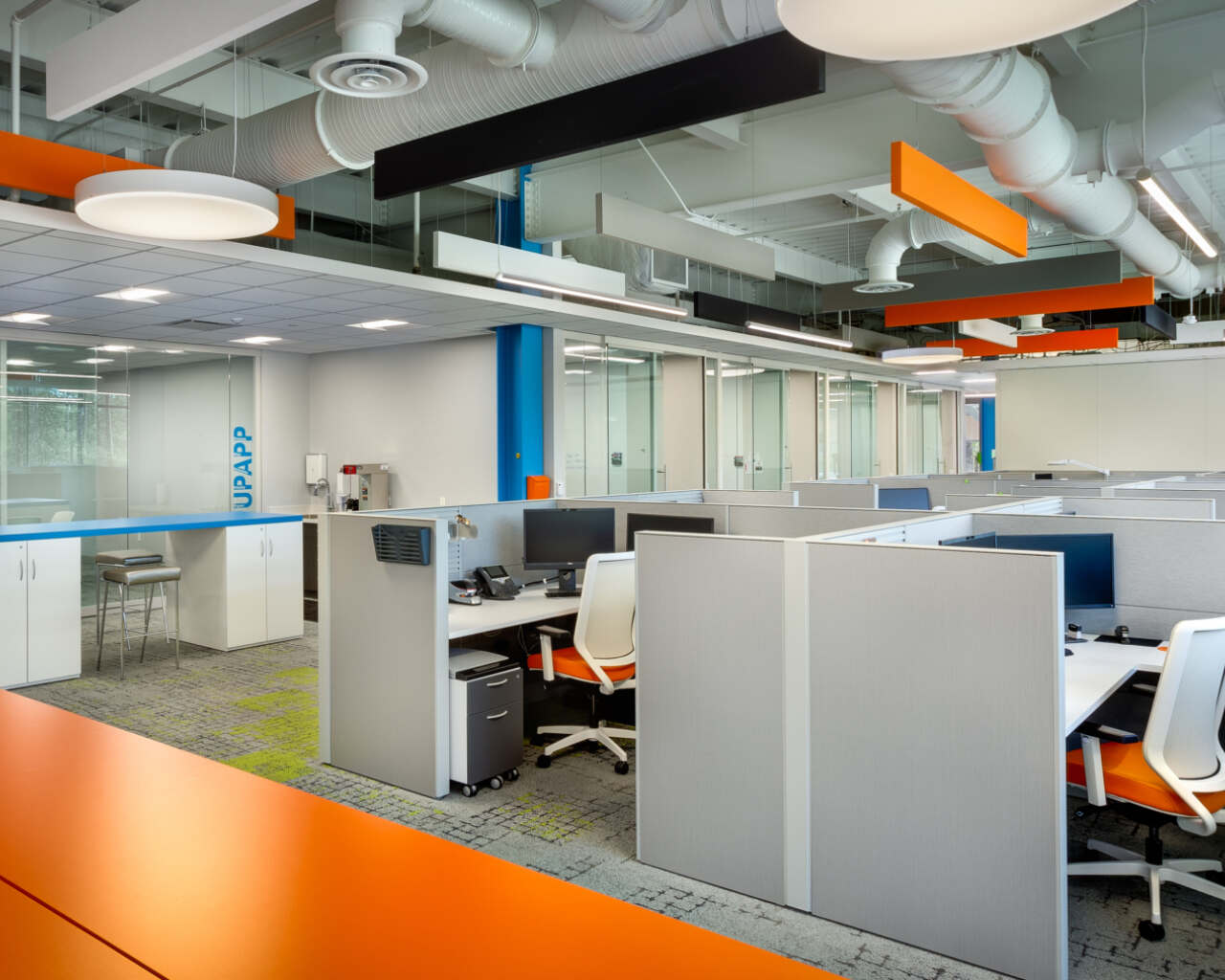
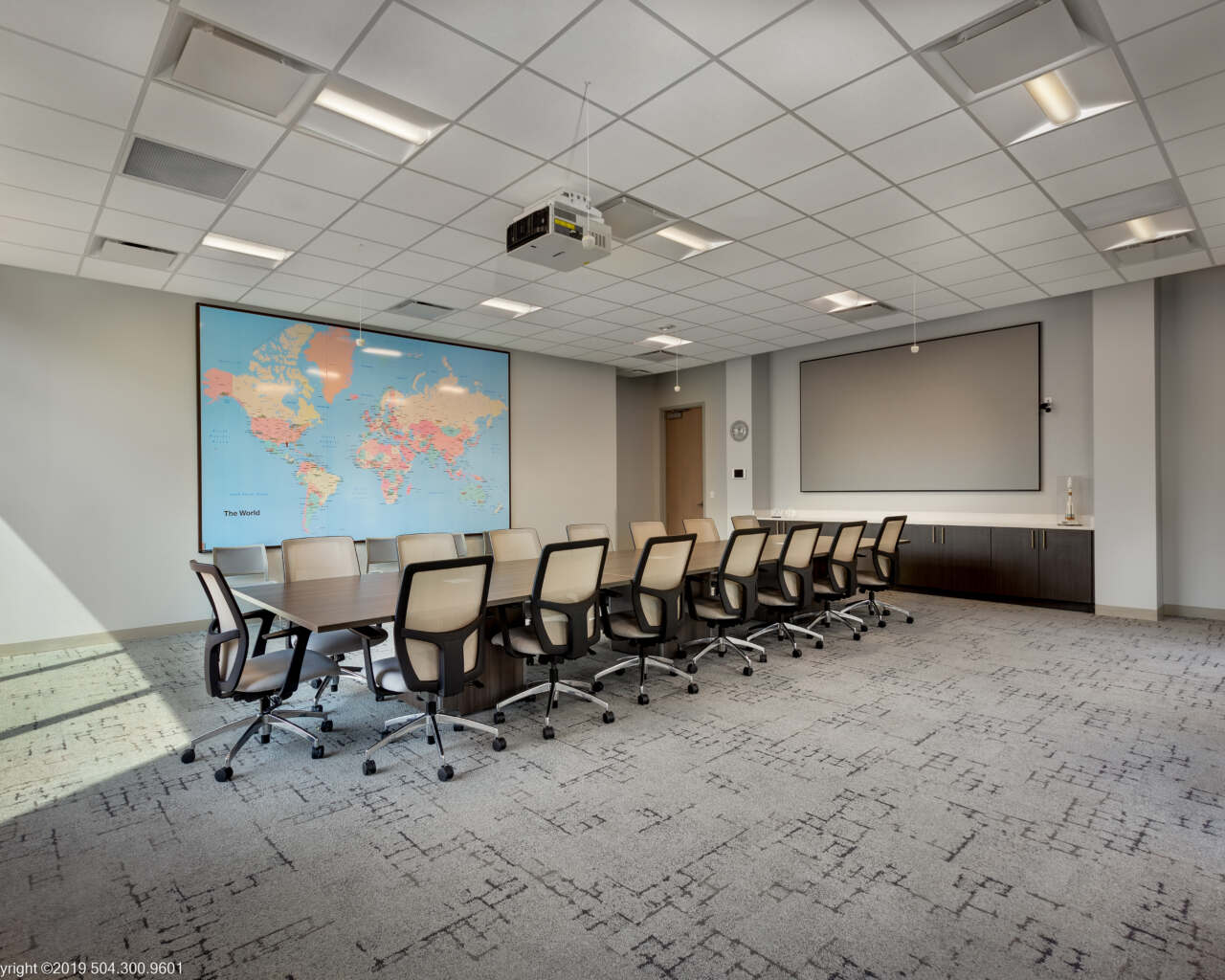
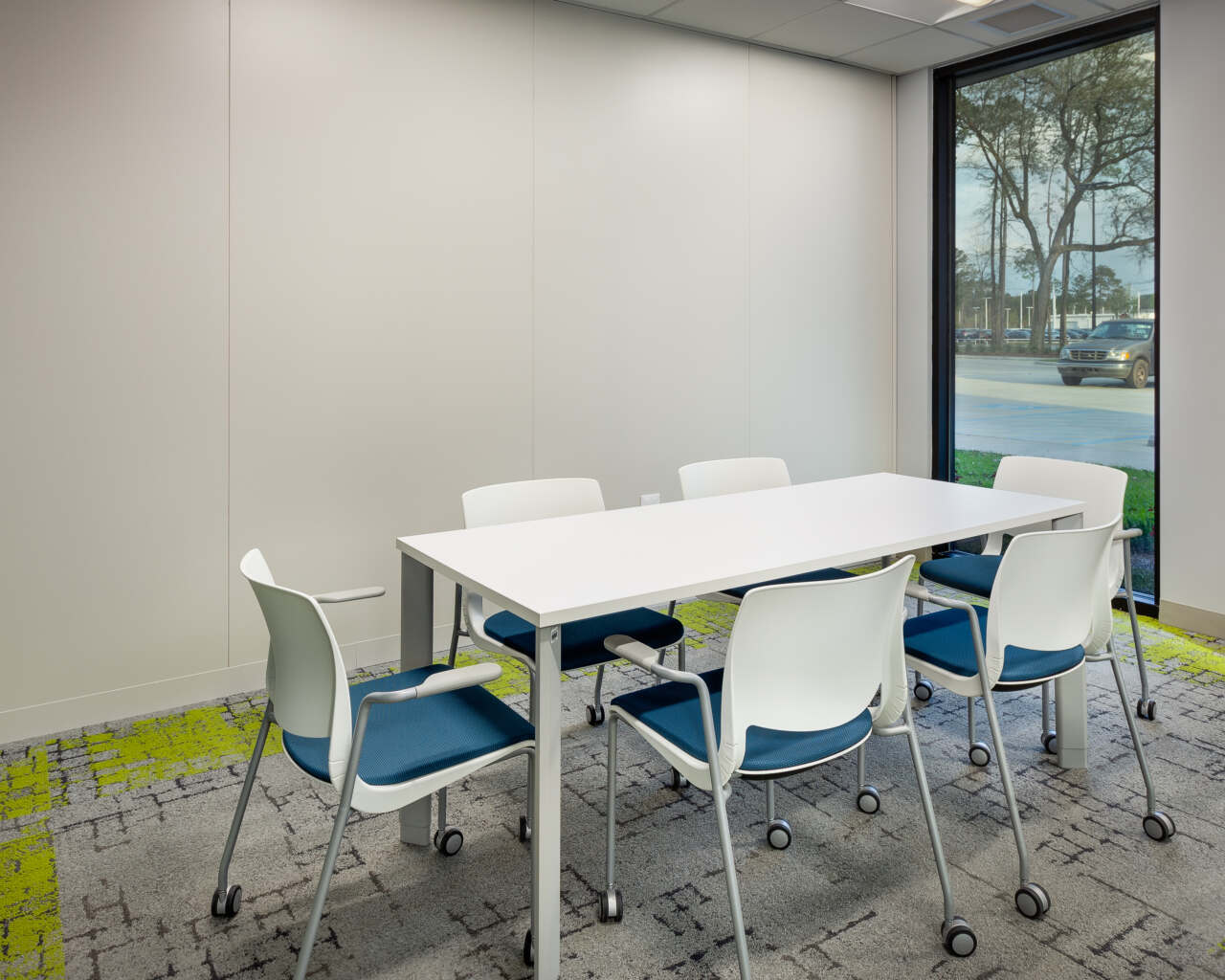
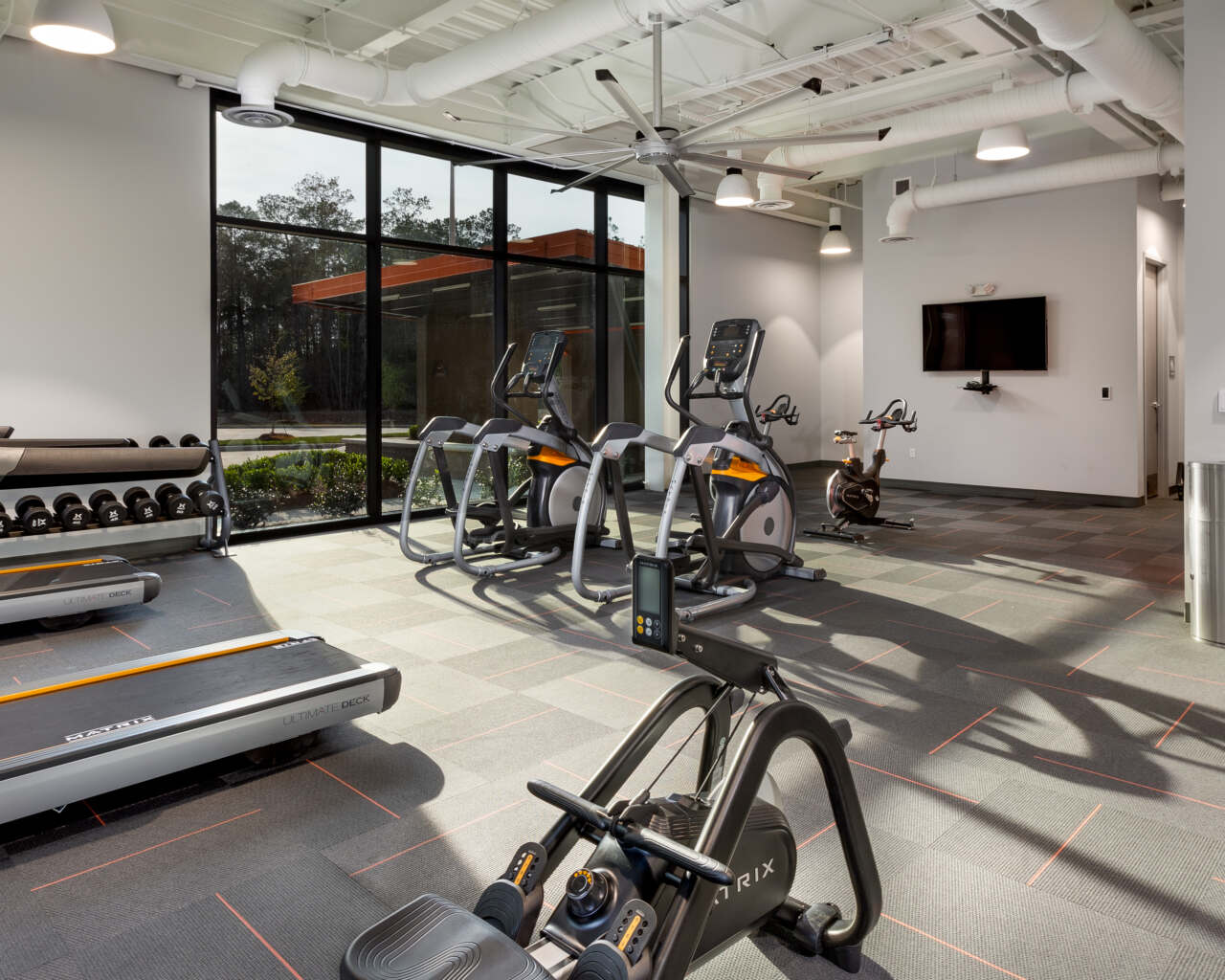
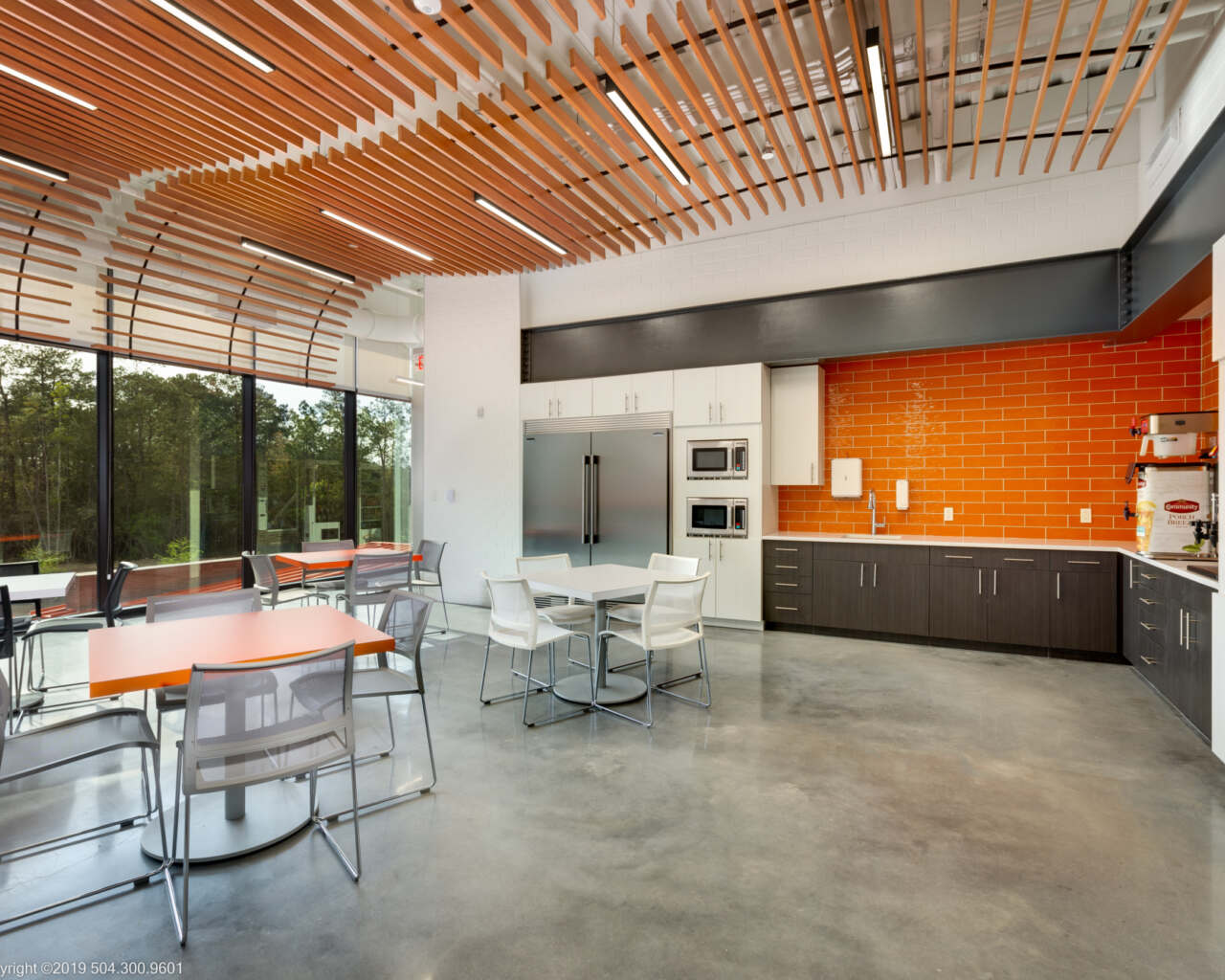
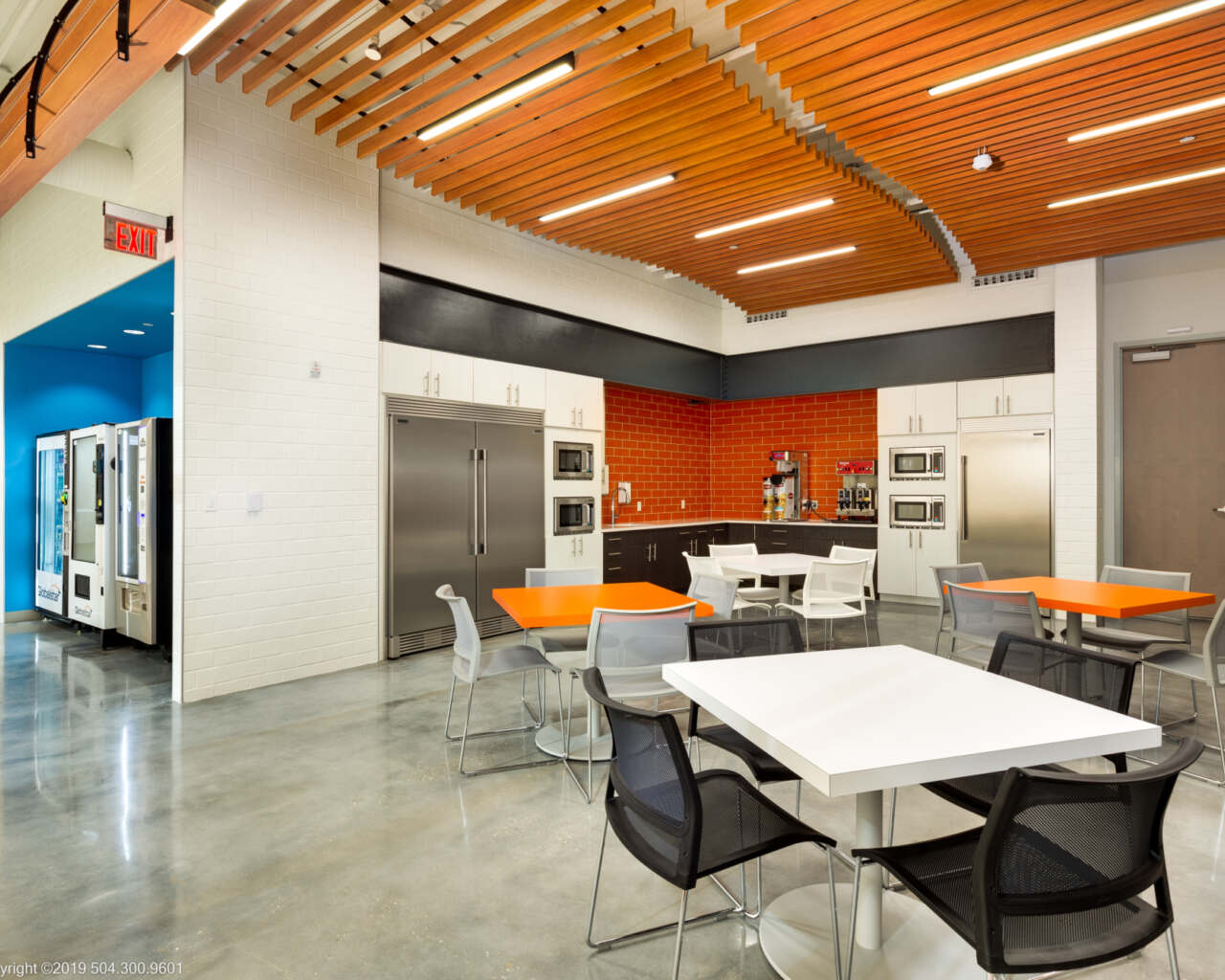
The project management, construction, submittal, and billing processes were seamless. Your team while multifunctional moves and constructs as one. Coordinating subs, working with architects, engineers, and all our own sub-contractors, from cablers, to furniture, your team treated each component as one consolidated effort, never ever shifting responsibility.
Vicky Gehbauer, Sr. Director Corporate Facilities and Wellness
Globalstar